Molde para Injetora Plástica: Como Escolher o Ideal para Sua Produção
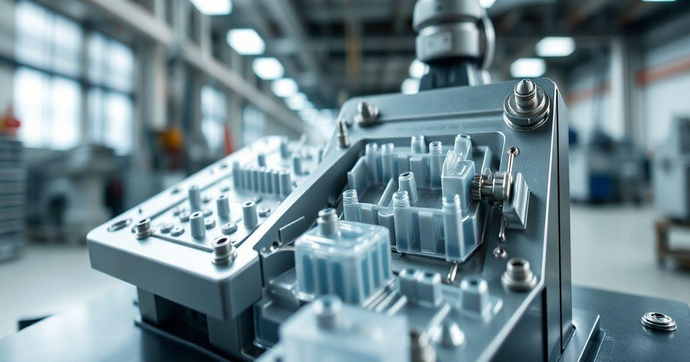
Por: Leonardo - 22 de Janeiro de 2025
O uso de moldes para injetora plástica é fundamental na indústria de transformação de plásticos, pois determina a qualidade e a eficiência da produção. Com a crescente demanda por produtos plásticos personalizados e de alta qualidade, escolher o molde adequado se torna uma tarefa crucial. Neste artigo, abordaremos os diferentes tipos de moldes, fatores a serem considerados na escolha, e as vantagens de investir em soluções personalizadas para otimizar sua produção.
Tipos de Moldes para Injetora Plástica e Suas Aplicações
Os moldes para injetora plástica são componentes essenciais na fabricação de produtos plásticos, permitindo a produção em massa de peças com alta precisão e repetibilidade. Existem diversos tipos de moldes, cada um projetado para atender a necessidades específicas de produção. A seguir, exploraremos os principais tipos de moldes para injetora plástica e suas aplicações.
Um dos tipos mais comuns de moldes é o molde de injeção de duas partes. Este tipo é composto por duas metades que se juntam durante o processo de injeção. Quando o plástico derretido é injetado, ele preenche o espaço entre as duas partes do molde, formando a peça desejada. Os moldes de duas partes são amplamente utilizados na produção de peças plásticas simples, como tampas, caixas e componentes automotivos. Sua versatilidade e eficiência os tornam uma escolha popular entre as empresas de injeção plástica.
Outro tipo importante é o molde de injeção de múltiplas cavidades. Este molde possui várias cavidades, permitindo a produção simultânea de várias peças em uma única injeção. Essa abordagem é ideal para aumentar a eficiência e reduzir os custos de produção, especialmente em aplicações de alta demanda. Moldes de múltiplas cavidades são frequentemente utilizados na fabricação de produtos como copos descartáveis, brinquedos e componentes eletrônicos. A capacidade de produzir várias peças de uma só vez torna esses moldes uma escolha atraente para empresas que buscam maximizar sua produtividade.
Os moldes de injeção de núcleo e cavidade são outra categoria importante. Esses moldes são projetados para criar formas complexas e detalhes intrincados nas peças plásticas. O núcleo é a parte do molde que cria a parte interna da peça, enquanto a cavidade forma a parte externa. Esse tipo de molde é frequentemente utilizado na produção de peças que exigem alta precisão e detalhes, como componentes médicos e peças de máquinas. A complexidade do design desses moldes pode aumentar os custos, mas a qualidade das peças produzidas justifica o investimento.
Além disso, existem os moldes de injeção de compressão, que são utilizados principalmente para materiais plásticos termofixos. Nesse processo, o material é colocado no molde antes de ser aquecido e comprimido, permitindo que ele se expanda e preencha o molde. Os moldes de compressão são frequentemente utilizados na fabricação de peças elétricas, isoladores e componentes automotivos. Embora não sejam tão comuns quanto os moldes de injeção tradicionais, eles desempenham um papel importante em aplicações específicas.
Os moldes de injeção de sopro são utilizados para produzir peças ocas, como garrafas e recipientes. Nesse processo, o plástico derretido é injetado em um molde e, em seguida, um ar comprimido é soprado para expandir o material, formando a peça oca. Esse tipo de molde é amplamente utilizado na indústria de embalagens, onde a produção em massa de garrafas plásticas é uma necessidade. A eficiência e a capacidade de produzir peças leves e resistentes tornam os moldes de sopro uma escolha popular.
Por fim, os moldes de injeção de tecnologia de cavidade quente são projetados para manter o material plástico aquecido durante todo o processo de injeção. Isso ajuda a reduzir o tempo de ciclo e melhora a qualidade das peças produzidas. Moldes de cavidade quente são frequentemente utilizados em aplicações que exigem alta qualidade superficial e precisão dimensional, como na indústria automotiva e eletrônica. Embora esses moldes possam ser mais caros, os benefícios em termos de eficiência e qualidade podem compensar o investimento inicial.
Em resumo, a escolha do tipo de molde para injetora plástica depende das necessidades específicas de produção, incluindo o tipo de material, a complexidade da peça e a quantidade a ser produzida. Compreender as diferentes opções disponíveis permite que as empresas selecionem o molde mais adequado para suas operações, garantindo eficiência e qualidade na produção de peças plásticas.
Fatores a Considerar na Escolha do Molde Ideal
A escolha do molde ideal para injetora plástica é um passo crucial no processo de fabricação de peças plásticas. Um molde bem projetado não apenas garante a qualidade das peças, mas também influencia diretamente a eficiência da produção e os custos envolvidos. Existem diversos fatores que devem ser considerados ao selecionar o molde mais adequado para suas necessidades. A seguir, discutiremos os principais aspectos a serem levados em conta.
Um dos primeiros fatores a considerar é o material do molde. Os moldes podem ser fabricados a partir de diferentes materiais, como aço, alumínio ou até mesmo materiais compostos. O aço é frequentemente escolhido por sua durabilidade e resistência ao desgaste, tornando-o ideal para produções em larga escala. Por outro lado, os moldes de alumínio são mais leves e podem ser mais econômicos, mas tendem a ter uma vida útil menor. A escolha do material deve levar em conta a quantidade de peças a serem produzidas, o tipo de plástico a ser utilizado e o orçamento disponível.
Outro aspecto importante é a complexidade do design da peça. Peças com geometrias complexas ou detalhes intrincados exigem moldes mais sofisticados, que podem aumentar os custos de produção. É fundamental avaliar se o molde pode ser fabricado de forma eficiente e se a tecnologia disponível na ferramentaria de moldes plasticos é capaz de atender às especificações necessárias. Moldes que exigem alta precisão e detalhes finos podem demandar um investimento maior, mas são essenciais para garantir a qualidade do produto final.
A quantidade de produção também é um fator determinante na escolha do molde. Para produções em larga escala, é recomendável optar por moldes de alta durabilidade, que suportem um maior número de ciclos de injeção. Já para produções menores ou protótipos, moldes de alumínio ou até mesmo moldes impressos em 3D podem ser uma alternativa viável e mais econômica. Avaliar a demanda de produção ajudará a decidir qual tipo de molde é mais adequado para o projeto.
Além disso, a facilidade de manutenção do molde deve ser considerada. Moldes que são difíceis de limpar ou que exigem manutenção complexa podem aumentar os custos operacionais e o tempo de inatividade da produção. É importante escolher um molde que permita acesso fácil a todas as suas partes, facilitando a limpeza e a manutenção regular. Moldes bem projetados não apenas garantem a eficiência da produção, mas também prolongam a vida útil do equipamento.
Outro fator a ser considerado é a temperatura de injeção. Diferentes tipos de plásticos requerem temperaturas específicas para serem processados adequadamente. O molde deve ser capaz de suportar essas temperaturas sem deformações ou danos. Moldes que não são projetados para as temperaturas necessárias podem resultar em peças defeituosas e aumentar os custos de produção. Portanto, é essencial verificar as especificações do material plástico a ser utilizado e garantir que o molde escolhido seja compatível.
A configuração do sistema de injeção também desempenha um papel importante na escolha do molde. O tipo de injetora utilizada, a pressão de injeção e a velocidade de injeção são fatores que influenciam o design do molde. Moldes projetados para sistemas de injeção específicos podem melhorar a eficiência e a qualidade da produção. É recomendável consultar especialistas em moldes e injeção para garantir que o molde atenda às especificações do sistema de injeção que será utilizado.
Por fim, a custo-benefício deve ser avaliada. Embora seja tentador optar por moldes mais baratos, é importante considerar o impacto a longo prazo na qualidade e na eficiência da produção. Investir em um molde de qualidade pode resultar em economia de custos operacionais e maior satisfação do cliente. Portanto, é fundamental equilibrar o custo inicial do molde com os benefícios que ele proporcionará ao longo do tempo.
Em resumo, a escolha do molde ideal para injetora plástica envolve uma análise cuidadosa de diversos fatores, incluindo o material do molde, a complexidade do design, a quantidade de produção, a facilidade de manutenção, a temperatura de injeção, a configuração do sistema de injeção e o custo-benefício. Considerar esses aspectos ajudará a garantir que o molde escolhido atenda às necessidades específicas de produção, resultando em peças plásticas de alta qualidade e eficiência.
Processo de Fabricação de Moldes para Injetora Plástica
A fabricação de moldes para injetora plástica é um processo complexo que envolve várias etapas, desde o design inicial até a produção final do molde. Cada fase é crucial para garantir que o molde atenda às especificações necessárias e produza peças plásticas de alta qualidade. A seguir, detalharemos as principais etapas do processo de fabricação de moldes para injetora plástica.
O primeiro passo no processo é a definição do projeto do molde. Nesta fase, engenheiros e designers trabalham juntos para criar um modelo 3D do molde, utilizando software de CAD (Desenho Assistido por Computador). O design deve levar em consideração a geometria da peça a ser produzida, as características do material plástico e as especificações da injetora. Um bom projeto é fundamental, pois erros nesta fase podem resultar em moldes ineficientes ou até mesmo inviáveis. A colaboração entre as equipes de design e produção é essencial para garantir que todas as necessidades sejam atendidas.
Após a finalização do projeto, a próxima etapa é a fabricação do molde. Essa fase envolve a usinagem das peças do molde a partir de materiais como aço ou alumínio. A ferramentaria e usinagem desempenham um papel crucial nesta etapa, pois as máquinas CNC (Controle Numérico Computadorizado) são utilizadas para cortar e moldar o material de acordo com as especificações do projeto. A precisão das máquinas CNC garante que as peças do molde sejam fabricadas com alta exatidão, o que é vital para o funcionamento adequado do molde durante a injeção.
Uma vez que as peças do molde são usinadas, elas passam por um processo de montagem. Nesta fase, as diferentes partes do molde são unidas, incluindo a cavidade e o núcleo. A montagem deve ser realizada com cuidado, pois qualquer desalinhamento pode afetar a qualidade das peças produzidas. Além disso, é importante garantir que todas as partes móveis do molde estejam funcionando corretamente, permitindo que o molde se abra e feche de maneira eficiente.
Após a montagem, o molde passa por um processo de tratamento térmico. Este tratamento é realizado para aumentar a dureza e a resistência do material, prolongando a vida útil do molde. O tratamento térmico pode incluir processos como têmpera e revenimento, que ajudam a melhorar as propriedades mecânicas do molde. Essa etapa é especialmente importante para moldes que serão utilizados em produções de alta demanda, onde o desgaste é uma preocupação constante.
Uma vez que o tratamento térmico é concluído, o molde é submetido a um processo de acabamento. O acabamento envolve a aplicação de técnicas como polimento e revestimento, que melhoram a superfície do molde e garantem que as peças plásticas produzidas tenham uma boa qualidade superficial. Um acabamento adequado também ajuda a reduzir o atrito durante o processo de injeção, facilitando a operação do molde e melhorando a eficiência da produção.
Após o acabamento, o molde é testado em um processo conhecido como teste de injeção. Durante este teste, o molde é colocado na injetora e um material plástico é injetado para verificar se o molde está funcionando corretamente. O teste permite identificar possíveis problemas, como vazamentos ou falhas na formação da peça. Se forem encontrados problemas, ajustes podem ser feitos antes que o molde entre em produção em larga escala. Essa fase é crucial para garantir que o molde atenda a todas as especificações e produza peças de alta qualidade.
Finalmente, após a aprovação do teste de injeção, o molde está pronto para ser utilizado na produção em massa. A fabricação de moldes para injetora plástica é um processo que exige atenção aos detalhes e um alto nível de precisão em cada etapa. A qualidade do molde final terá um impacto direto na eficiência da produção e na qualidade das peças plásticas produzidas.
Em resumo, o processo de fabricação de moldes para injetora plástica envolve várias etapas, incluindo o design do molde, a usinagem, a montagem, o tratamento térmico, o acabamento e o teste de injeção. Cada uma dessas fases é essencial para garantir que o molde atenda às especificações necessárias e produza peças plásticas de alta qualidade. Investir tempo e recursos em um processo de fabricação bem estruturado é fundamental para o sucesso na produção de peças plásticas.
Vantagens de Utilizar Moldes Personalizados
A utilização de moldes personalizados na fabricação de peças plásticas oferece uma série de vantagens significativas que podem impactar positivamente a eficiência da produção e a qualidade dos produtos finais. Moldes personalizados são projetados especificamente para atender às necessidades de um projeto ou produto, permitindo uma abordagem mais flexível e adaptável. A seguir, discutiremos as principais vantagens de optar por moldes personalizados.
Uma das principais vantagens de utilizar moldes personalizados é a eficiência na produção. Moldes feitos sob medida são projetados para otimizar o processo de injeção, permitindo que as peças sejam produzidas de forma mais rápida e com menos desperdício de material. Isso se traduz em ciclos de produção mais curtos e maior produtividade. Quando comparados a moldes padrão, os moldes personalizados podem reduzir significativamente o tempo de injeção e o tempo de resfriamento, resultando em uma produção mais eficiente e econômica.
Além disso, os moldes personalizados permitem a criação de peças com geometria complexa e detalhes intrincados que podem ser difíceis de alcançar com moldes padrão. Isso é especialmente importante em indústrias que exigem alta precisão e qualidade, como a automotiva, eletrônica e médica. Com um molde personalizado, é possível projetar peças que atendam a especificações rigorosas, garantindo que o produto final atenda aos padrões de qualidade exigidos pelo mercado. Essa flexibilidade no design é uma das razões pelas quais muitas empresas optam por moldes personalizados.
Outra vantagem significativa é a redução de custos a longo prazo. Embora o investimento inicial em um molde personalizado possa ser maior do que em um molde padrão, a economia gerada ao longo do tempo pode ser substancial. Moldes personalizados são projetados para durar mais e suportar um maior número de ciclos de injeção, o que significa que as empresas podem economizar em custos de manutenção e substituição. Além disso, a produção mais eficiente e a redução do desperdício de material contribuem para a diminuição dos custos operacionais, tornando a opção de moldes personalizados mais atraente a longo prazo.
A qualidade do produto final também é uma consideração importante. Moldes personalizados permitem um controle mais rigoroso sobre o processo de injeção, resultando em peças com melhor acabamento superficial e dimensões mais precisas. Isso é crucial em setores onde a qualidade é fundamental, como na fabricação de componentes eletrônicos ou peças automotivas. A capacidade de produzir peças de alta qualidade não apenas melhora a satisfação do cliente, mas também pode aumentar a reputação da empresa no mercado.
Além disso, a utilização de moldes personalizados pode proporcionar uma maior flexibilidade de design. À medida que as necessidades do mercado mudam, as empresas podem precisar adaptar seus produtos para atender a novas demandas. Com moldes personalizados, é mais fácil fazer ajustes e modificações no design das peças, permitindo que as empresas se adaptem rapidamente às mudanças nas preferências dos consumidores ou nas exigências do mercado. Essa agilidade é uma vantagem competitiva significativa em um ambiente de negócios em constante evolução.
Os moldes personalizados também oferecem a possibilidade de inovações tecnológicas. Ao trabalhar com um fabricante de moldes que compreende as últimas tendências e tecnologias, as empresas podem incorporar recursos avançados em seus moldes, como sistemas de resfriamento eficientes, mecanismos de extração automatizados e sensores de monitoramento. Essas inovações podem melhorar ainda mais a eficiência da produção e a qualidade das peças, proporcionando uma vantagem adicional sobre a concorrência.
Outro aspecto a ser considerado é a redução do tempo de desenvolvimento de produtos. Com moldes personalizados, as empresas podem acelerar o processo de desenvolvimento de novos produtos, uma vez que os moldes são projetados especificamente para atender às necessidades do projeto. Isso significa que as empresas podem levar seus produtos ao mercado mais rapidamente, o que é crucial em setores onde a velocidade é um fator determinante para o sucesso.
Por fim, a utilização de moldes personalizados pode resultar em uma maior satisfação do cliente. Quando as empresas conseguem produzir peças que atendem exatamente às especificações dos clientes, a probabilidade de satisfação aumenta. Isso não apenas fortalece o relacionamento com os clientes existentes, mas também pode atrair novos clientes que buscam soluções personalizadas para suas necessidades. A capacidade de oferecer produtos de alta qualidade e personalizados é um diferencial competitivo que pode impulsionar o crescimento dos negócios.
Em resumo, as vantagens de utilizar moldes personalizados na fabricação de peças plásticas são numerosas e impactantes. Desde a eficiência na produção e a criação de peças complexas até a redução de custos a longo prazo e a melhoria da qualidade do produto final, os moldes personalizados oferecem uma solução adaptável e eficaz para atender às necessidades específicas de cada projeto. Com a crescente demanda por produtos personalizados e de alta qualidade, investir em moldes personalizados é uma estratégia inteligente para empresas que desejam se destacar no mercado.
Manutenção e Cuidados com Moldes para Injetora Plástica
A manutenção adequada e os cuidados com moldes para injetora plástica são essenciais para garantir a eficiência e a durabilidade desses equipamentos. Moldes bem mantidos não apenas prolongam a vida útil, mas também asseguram a qualidade das peças produzidas. A seguir, discutiremos as melhores práticas de manutenção e cuidados que devem ser adotados para otimizar o desempenho dos moldes.
Um dos primeiros passos na manutenção de moldes é a limpeza regular. Após cada ciclo de produção, é fundamental realizar uma limpeza minuciosa do molde. Resíduos de plástico, poeira e outros contaminantes podem se acumular e afetar a qualidade das peças. Utilize um pano macio e produtos de limpeza adequados para remover qualquer resíduo. Evite o uso de solventes agressivos que possam danificar o molde. A limpeza deve ser parte integrante da rotina de manutenção, garantindo que o molde esteja sempre em condições ideais para a produção.
Além da limpeza, a lubrificação é um aspecto crucial na manutenção de moldes. As partes móveis do molde, como pinos e eixos, devem ser lubrificadas regularmente para evitar o desgaste e garantir um funcionamento suave. A falta de lubrificação pode levar a falhas mecânicas e a um aumento do atrito, resultando em danos ao molde. Utilize lubrificantes recomendados pelo fabricante e siga as instruções para a aplicação correta. A lubrificação deve ser realizada de acordo com a frequência de uso do molde e as recomendações do fabricante.
Outro cuidado importante é a verificação das condições do molde. Inspecione regularmente o molde em busca de sinais de desgaste, corrosão ou danos. Fique atento a fissuras, quebras ou deformações que possam comprometer a qualidade das peças produzidas. Caso identifique algum problema, é fundamental realizar os reparos necessários imediatamente. Ignorar pequenos danos pode levar a problemas maiores e mais custosos no futuro. A manutenção preventiva é sempre mais econômica do que a correção de falhas graves.
A temperatura de operação também deve ser monitorada. Moldes que operam em temperaturas inadequadas podem sofrer deformações e danos. É importante garantir que o sistema de resfriamento do molde esteja funcionando corretamente, especialmente em processos de injeção que geram altas temperaturas. Verifique regularmente as condições do sistema de resfriamento e faça ajustes conforme necessário. Um controle adequado da temperatura ajuda a manter a integridade do molde e a qualidade das peças.
Além disso, a armazenagem adequada dos moldes quando não estão em uso é fundamental. Moldes devem ser armazenados em locais limpos, secos e protegidos de umidade e poeira. Utilize capas protetoras para evitar a entrada de contaminantes e mantenha os moldes em posição vertical ou em suportes adequados para evitar deformações. A forma como os moldes são armazenados pode impactar diretamente sua durabilidade e desempenho quando forem utilizados novamente.
É recomendável também realizar inspeções periódicas por profissionais qualificados. Técnicos especializados podem identificar problemas que podem passar despercebidos e realizar manutenções mais complexas, como ajustes e reparos. A contratação de serviços de manutenção preventiva pode ser uma estratégia eficaz para garantir que os moldes permaneçam em condições ideais de operação. Além disso, esses profissionais podem oferecer orientações sobre as melhores práticas de manutenção e cuidados específicos para cada tipo de molde.
Outro aspecto a ser considerado é a documentação e registro de manutenção. Manter um registro detalhado das atividades de manutenção realizadas, incluindo limpezas, lubrificações e reparos, pode ser útil para monitorar o desempenho do molde ao longo do tempo. Essa documentação pode ajudar a identificar padrões de desgaste e a programar manutenções futuras de forma mais eficaz. Além disso, ter um histórico de manutenção pode ser valioso em caso de auditorias ou avaliações de qualidade.
Por fim, a educação e treinamento da equipe que opera os moldes são essenciais. Garantir que os operadores estejam cientes das melhores práticas de manutenção e cuidados com os moldes pode prevenir danos e aumentar a eficiência da produção. Realizar treinamentos regulares e fornecer informações sobre a importância da manutenção adequada pode resultar em uma operação mais segura e produtiva.
Em resumo, a manutenção e os cuidados com moldes para injetora plástica são fundamentais para garantir a eficiência, a qualidade e a durabilidade desses equipamentos. A limpeza regular, a lubrificação, a verificação das condições do molde, o monitoramento da temperatura, a armazenagem adequada, as inspeções periódicas, a documentação de manutenção e o treinamento da equipe são práticas essenciais que devem ser adotadas. Investir tempo e recursos na manutenção adequada dos moldes é uma estratégia inteligente que pode resultar em economia e maior satisfação do cliente.
Tendências e Inovações em Moldes para Injetoras Plásticas
O setor de injeção plástica está em constante evolução, impulsionado por inovações tecnológicas e mudanças nas demandas do mercado. As tendências atuais em moldes para injetoras plásticas refletem a necessidade de maior eficiência, sustentabilidade e personalização. Neste artigo, exploraremos as principais tendências e inovações que estão moldando o futuro da fabricação de moldes para injetoras plásticas.
Uma das tendências mais significativas é a automação e digitalização dos processos de fabricação de moldes. A introdução de tecnologias como a Internet das Coisas (IoT) e a Indústria 4.0 está transformando a maneira como os moldes são projetados, fabricados e mantidos. Sensores inteligentes podem ser integrados aos moldes para monitorar condições operacionais em tempo real, como temperatura e pressão, permitindo ajustes automáticos que melhoram a eficiência e a qualidade da produção. Essa automação não apenas reduz a necessidade de intervenção manual, mas também minimiza erros e aumenta a produtividade.
Outra inovação importante é o uso de materiais avançados na fabricação de moldes. Novos compostos e ligas metálicas estão sendo desenvolvidos para oferecer maior resistência ao desgaste e à corrosão, prolongando a vida útil dos moldes. Além disso, materiais como plásticos de engenharia e compósitos estão sendo utilizados para criar moldes mais leves e eficientes. Esses materiais avançados permitem a produção de peças com maior precisão e qualidade, atendendo às exigências crescentes do mercado.
A impressão 3D também está ganhando destaque na fabricação de moldes. Essa tecnologia permite a criação rápida de protótipos e moldes personalizados, reduzindo significativamente o tempo de desenvolvimento. A impressão 3D possibilita a produção de geometrias complexas que seriam difíceis ou impossíveis de alcançar com métodos tradicionais. Além disso, a capacidade de produzir moldes sob demanda reduz a necessidade de grandes estoques, tornando o processo mais ágil e econômico.
As soluções sustentáveis estão se tornando cada vez mais relevantes na indústria de injeção plástica. A crescente preocupação com o meio ambiente está levando as empresas a buscar alternativas mais ecológicas na fabricação de moldes. Isso inclui o uso de materiais recicláveis e a implementação de processos que minimizam o desperdício. Além disso, a eficiência energética dos moldes e das injetoras está sendo aprimorada, contribuindo para a redução da pegada de carbono da produção. Moldes que permitem a reciclagem de resíduos plásticos também estão se tornando populares, alinhando-se às práticas de economia circular.
A personalização em massa é outra tendência que está moldando o futuro dos moldes para injetoras plásticas. À medida que os consumidores exigem produtos mais personalizados, as empresas estão se adaptando para atender a essas demandas. Moldes personalizados permitem a produção de peças únicas ou em pequenas quantidades, sem comprometer a eficiência. Essa flexibilidade é crucial em setores como o de eletrônicos e automotivo, onde a personalização é cada vez mais valorizada. A capacidade de produzir moldes que atendam a especificações específicas do cliente é uma vantagem competitiva significativa.
Além disso, a integração de tecnologias de simulação está se tornando uma prática comum no design de moldes. Softwares de simulação permitem que os engenheiros testem virtualmente o desempenho do molde antes da fabricação, identificando possíveis problemas e otimizando o design. Isso não apenas economiza tempo e recursos, mas também melhora a qualidade do produto final. A simulação ajuda a prever o comportamento do material durante o processo de injeção, permitindo ajustes que garantem a eficiência e a precisão.
Por fim, a colaboração entre empresas e fornecedores está se intensificando. As parcerias estratégicas entre fabricantes de moldes e empresas de injeção plástica estão se tornando comuns, permitindo a troca de conhecimentos e experiências. Essa colaboração resulta em inovações mais rápidas e na implementação de soluções que atendem às necessidades específicas do mercado. Trabalhar em conjunto com fornecedores pode levar a melhorias significativas na qualidade e na eficiência dos moldes, beneficiando toda a cadeia de produção.
Em resumo, as tendências e inovações em moldes para injetoras plásticas estão moldando o futuro da indústria de injeção plástica. A automação, o uso de materiais avançados, a impressão 3D, as soluções sustentáveis, a personalização em massa, a integração de tecnologias de simulação e a colaboração entre empresas são algumas das principais forças que impulsionam essa evolução. À medida que o mercado continua a mudar, as empresas que adotam essas inovações estarão melhor posicionadas para atender às demandas dos consumidores e se destacar em um ambiente competitivo.
Em conclusão, a escolha e o uso adequados de moldes para injetora plástica são essenciais para garantir a qualidade e a eficiência na produção de peças plásticas. À medida que a indústria evolui, as inovações e tendências emergentes oferecem novas oportunidades para otimizar processos e atender às crescentes demandas do mercado. Investir em moldes personalizados, manter uma rotina de cuidados e estar atento às novas tecnologias são passos fundamentais para se destacar em um setor competitivo. Com as informações apresentadas, as empresas podem tomar decisões mais informadas e estratégicas, assegurando que seus produtos atendam aos mais altos padrões de qualidade e eficiência.