Produção de Moldes: Guia Completo para Iniciantes
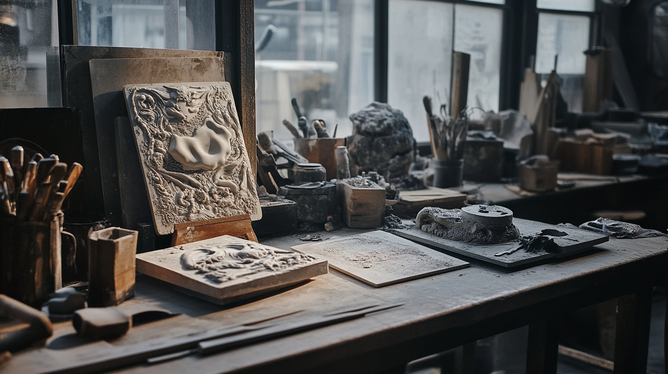
Por: Leonardo - 22 de Novembro de 2024
A produção de moldes é uma etapa crucial em diversos processos industriais, permitindo a fabricação precisa de peças em diferentes materiais. Neste artigo, abordaremos a importância da produção de moldes, os tipos disponíveis e as melhores práticas para otimizar esse processo. Se você busca aumentar a eficiência e a qualidade na sua produção, continue lendo e descubra dicas valiosas.
Importância da Produção de Moldes
A produção de moldes desempenha um papel fundamental em diversos setores industriais, sendo uma atividade que influencia diretamente a qualidade, eficiência e custo dos produtos finais. Os moldes são utilizados em processos de fabricação como injeção, fundição, extrusão e compressão, onde a precisão na forma e dimensão é essencial. Neste contexto, entender a importância da produção de moldes é crucial para qualquer profissional envolvido na área de engenharia, design ou produção. Vamos explorar os principais aspectos que tornam essa prática indispensável.
Qualidade dos Produtos Finais
Um dos principais objetivos da produção de moldes é garantir a qualidade dos produtos finais. A precisão nos moldes assegura que as peças fabricadas tenham as dimensões corretas, evitando falhas que podem comprometer a funcionalidade do produto. Um molde mal feito pode resultar em peças defeituosas, que não atendem aos padrões exigidos, forçando as empresas a realizar retrabalho ou até mesmo descartar produtos. Isso gera um aumento nos custos e pode causar atrasos na entrega, prejudicando a reputação da empresa.
Eficiência do Processo de Produção
A produção de moldes também está diretamente relacionada à eficiência dos processos produtivos. Moldes bem projetados e fabricados possibilitam a produção em larga escala, reduzindo o tempo de ciclo na fabricação das peças. Quando um molde é capaz de produzir várias peças de uma só vez, o tempo e o custo por unidade diminuem significativamente. Isso é especialmente importante em indústrias que trabalham com alta demanda, como a automotive e eletrônica, onde a redução de custos e a maximização da produção são essenciais para a competitividade no mercado.
Redução de Custos de Produção
A produção de moldes impacta diretamente nos custos gerais de fabricação. Embora o investimento inicial na criação de um molde possa ser elevado, ele é compensado pela redução dos custos de produção em massa. Moldes de alta qualidade são duráveis e reduzem a necessidade de manutenção frequente, além de diminuir o desperdício de material durante o processo de fabricação. O uso eficiente de materiais e a longa vida útil dos moldes resultam em economias significativas a longo prazo.
Customização e Inovação de Produtos
A capacidade de produzir moldes sob medida permite que as empresas inovem e customizem seus produtos de acordo com as demandas do mercado. Moldes podem ser projetados para criar formatos específicos ou características únicas que atendem às necessidades dos consumidores. Essa flexibilidade é fundamental para a diferenciação de produtos em um mercado cada vez mais competitivo. Com um molde adaptável, as empresas podem testar e lançar novas ideias rapidamente, atendendo assim às tendências do consumidor que mudam constantemente.
Valorização da Marca
A qualidade dos produtos resultantes da produção de moldes também está relacionada à valorização da marca. Produtos bem elaborados e com ótimo acabamento proporcionam uma experiência positiva ao consumidor. Isso, por sua vez, fortalece a imagem da marca no mercado e pode levar à fidelização do cliente. Quando os consumidores percebem que uma marca é sinônimo de qualidade, estão mais propensos a escolher seus produtos em detrimento dos concorrentes.
Adaptação às Mudanças do Mercado
O ambiente industrial é dinâmico e está sempre em mudança. Novas tecnologias, materiais e métodos de produção são constantemente introduzidos. A produção de moldes permite que as empresas se adaptem rapidamente a essas mudanças. Com moldes atualizados e projetados para novos processos, as empresas podem incorporar inovações em seus produtos sem grandes reestruturações na linha de produção. Essa capacidade de adaptação é vital para a sobrevivência e sucesso das empresas nos dias atuais.
Papel na Sustentabilidade
A produção de moldes também desempenha um papel importante nas práticas sustentáveis dentro das indústrias. Moldes bem projetados podem reduzir o desperdício de material, diminuindo a pegada ambiental da produção. Além disso, a utilização de tecnologias mais eficientes na fabricação de moldes contribui para processos menos poluentes. A indústria, cada vez mais, busca por soluções que minimizem os impactos ambientais e, neste sentido, a produção de moldes não fica para trás.
Considerações Finais
Em resumo, a produção de moldes é uma etapa crítica em qualquer processo de fabricação que envolve a criação de peças de precisão. Ela impacta diretamente na qualidade do produto final, eficiência do processo, redução de custos, personalização, valorização da marca, adaptação às mudanças do mercado e práticas sustentáveis. Profissionais da indústria devem reconhecer a importância dessa prática e investir em tecnologias e processos que assegurem a produção de moldes de alta qualidade. A compreensão desses aspectos não apenas beneficia a empresa, mas também contribui para um mercado mais inovador e responsável.
Tipos de Molde e Suas Aplicações
A produção de moldes abrange uma variedade de tipos, cada um projetado para atender necessidades específicas em diferentes setores industriais. A escolha do molde adequado é fundamental, uma vez que cada tipo possui características que determinam a eficiência do processo produtivo e a qualidade do produto final. Neste artigo, exploraremos os principais tipos de moldes e suas aplicações, facilitando a compreensão sobre quando e como utilizar cada um deles.
Molde de Injeção
Os moldes de injeção são amplamente utilizados na indústria de plásticos e são essenciais para a fabricação de peças complexas e em grande escala. Este tipo de molde funciona através da injeção de plástico derretido em uma cavidade moldada, onde o material se solidifica e forma a peça final.
Uma das principais aplicações dos moldes de injeção é na produção de componentes para eletroeletrônicos, como caixas de dispositivos, peças de automóveis, brinquedos e utensílios de cozinha. A principal vantagem do molde de injeção é a capacidade de produzir uma alta quantidade de peças de forma rápida e com excelente acabamento superficial.
Molde de Compressão
Os moldes de compressão são tipicamente utilizados na fabricação de produtos de borracha e de plásticos termoelásticos. Este tipo de molde funciona por meio da compressão de material em um espaço vazio, resultando na formação do produto. O material é aquecido para torná-lo moldável, colocado na cavidade do molde, e, em seguida, a pressão e o calor são aplicados para finalizar o processo.
As principais aplicações incluem a produção de pneus, selos, mangueiras, e outros produtos que requerem resistência e flexibilidade. Os moldes de compressão são ideais para itens que exigem uma configuração específica ou formas personalizadas e são valorizados por seu baixo custo em comparação a outros métodos.
Molde de Extrusão
Os moldes de extrusão são utilizados para criar produtos longos e contínuos, como tubos, perfis e folhas plásticas. Neste processo, o material plástico é aquecido e empurrado através de um molde com a forma desejada. O produto extrudado é cortado nas dimensões apropriadas após a saída do molde.
Esse tipo de molde é bastante eficiente para a produção em massa, especialmente em indústrias que fornecem materiais para construção, embalagens e indústria de alimentos. As desvantagens incluem a necessidade de um investimento significativo em maquinário e a limitação em relação ao formato do produto final.
Molde de Fundição
Os moldes de fundição são utilizados para criar componentes metálicos ao derramar metal fundido em moldes com a forma desejada. Este tipo de molde pode ser feito de areia, metal ou outros materiais, e a escolha do material depende da temperatura do metal a ser utilizado e das características do produto final.
As aplicações de moldes de fundição são amplas, abrangendo setores como a fabricação de peças automotivas, componentes de máquinas e estruturas metálicas. A fundição permite a produção de peças com detalhes intricados e tamanhos variados, mas pode exigir processos adicionais de acabamento e tratamento para atingir as especificações desejadas.
Molde de Sopro
Os moldes de sopro são usados para criar objetos ocos a partir de plásticos, como garrafas e recipientes. O processo envolve a inserção de um tubo de plástico aquecido em um molde, onde o ar é soprado para expandir o plástico e moldá-lo na forma desejada.
A aplicação mais comum do molde de sopro é na indústria de embalagens, especialmente para garrafas PET, recipientes e outros produtos similares. Este processo é ideal para grandes produções e proporciona formas com alta qualidade superficial.
Molde de Termoformagem
Os moldes de termoformagem são utilizados para criar produtos de plástico a partir de folhas termoplásticas. Neste processo, a folha de plástico é aquecida e esticada sobre um molde, onde esfria e adquire a forma desejada.
A termoformagem é muito utilizada na fabricação de embalagens, painéis solares e itens de decoração. As principais vantagens desse tipo de molde são a flexibilidade em design e a capacidade de produzir itens de formas variadas com alta eficiência.
Molde de Rotomoldagem
Os moldes de rotomoldagem são utilizados para criar objetos ocos, como tanques de armazenamento, brinquedos e mobiliário urbano. Este processo envolve a adição de um pó plástico em um molde, que é então aquecido e girado para permitir que o material derretido se adira às paredes do molde.
A rotomoldagem é conhecida por permitir a produção de peças grandes e complexas, sendo especialmente utilizada na indústria de plásticos industriais. Ela é eficiente em termos de custo e energia, especialmente para produções em menor escala.
Molde de Fabricação Aditiva (Impressão 3D)
A impressão 3D, ou moldagem aditiva, é uma tecnologia emergente que utiliza moldes digitais para criar objetos camada por camada. Essa técnica tem se tornado cada vez mais popular na produção de protótipos e peças personalizadas.
As aplicações incluem desde protótipos de design até componentes finais para setores como medicina e aeroespacial. A principal vantagem é a capacidade de criar formas complexas que seriam quase impossíveis de serem produzidas com métodos tradicionais. Além disso, a impressão 3D oferece uma redução significativa de desperdício em comparação com métodos subtrativos.
Considerações Finais Sobre os Tipos de Moldes
A escolha do tipo de molde a ser utilizado depende de diversos fatores, incluindo o material a ser moldado, a complexidade da peça, o volume de produção e os custos envolvidos. Cada tipo de molde tem suas particularidades e benefícios, e entender essas diferenças é essencial para otimizar a produção e garantir a qualidade dos produtos finais.
À medida que as tecnologias continuam a evoluir, novos métodos e tipos de moldes também estão sendo desenvolvidos, proporcionando ainda mais opções para fabricantes industriais. Portanto, é vital que os profissionais da área se mantenham atualizados sobre as tendências e inovações no campo da produção de moldes, garantindo que possam tomar decisões informadas para suas operações.
Passo a Passo na Produção de Moldes
A produção de moldes é um processo metódico e minucioso que permite a criação de peças com precisão e qualidade. Seguir um passo a passo bem definido é fundamental para garantir que os moldes atendam às especificações desejadas e funcionem corretamente durante a fabricação. Neste artigo, vamos explorar as etapas essenciais envolvidas na produção de moldes, desde o planejamento inicial até a finalização e testes. Acompanhe e descubra como realizar cada etapa de forma eficiente.
1. Planejamento e Design do Molde
A primeira etapa na produção de moldes é o planejamento e o design. Essa fase envolve a definição das especificações do molde, como o tipo de peça a ser produzido, o material do molde, e as condições de operação. É fundamental trabalhar em colaboração com engenheiros e designers para garantir que todos os requisitos sejam considerados.
O design do molde geralmente é realizado utilizando software CAD (Computer-Aided Design), que permite criar modelos tridimensionais do molde e da peça que será fabricada. Esses modelos ajudam a visualizar a interação entre o molde e o produto final e a detectar potenciais problemas antes da produção.
2. Seleção do Material do Molde
A escolha do material para fabricar o molde é crucial e depende de diversos fatores, como tipo de processo de produção, volume de produção e propriedades desejadas da peça. Os materiais mais comuns para moldes incluem aço, alumínio e bronze, cada um com suas características e aplicações específicas.
Os moldes de aço são duráveis e adequados para produções em larga escala, enquanto os moldes de alumínio são mais leves e mais fáceis de fabricar, mas podem ter uma vida útil menor. O bronze, por sua vez, é frequentemente usado em aplicação de alta resistência ao desgaste. A seleção do material adequado impactará diretamente na eficiência do processo e na qualidade do produto final.
3. Criação do Molde (Usinagem)
Após o design e a escolha do material, inicia-se a etapa de usinagem do molde. Essa fase envolve a transformação do material escolhido em um molde utilizável. As operações de usinagem podem incluir fresamento, torneamento, furação e retificação.
É essencial realizar esta etapa utilizando máquinas de alta precisão, garantindo que as dimensões do molde estejam de acordo com as especificações do projeto. Pequenos erros nessa fase podem levar a problemas a montante durante a fabricação das peças, resultando em produtos finais defeituosos.
4. Tratamento Térmico
Após a usinagem, o molde geralmente passa por um tratamento térmico para aumentar sua dureza e resistência ao desgaste. Esse processo envolve aquecer o molde a uma temperatura elevada e, em seguida, resfriá-lo rapidamente, alterando suas propriedades metálicas. O tratamento térmico pode incluir processos como têmpera, revenido e recozimento.
Essa etapa é essencial para garantir que o molde possa suportar as pressões e temperaturas envolvidas no processo de fabricação, prolongando sua vida útil e melhorando a qualidade do produto final.
5. Montagem do Molde
Após o tratamento térmico, o molde é montado. Essa fase envolve a união das diferentes partes do molde, garantindo que todas as peças estejam em conformidade e funcionem corretamente. É importante verificar o alinhamento e a vedação das partes, pois vazamentos ou desalinhamentos podem causar falhas na produção.
A montagem pode incluir a instalação de componentes adicionais, como dispositivos de resfriamento, sistemas de subida e descida, e outros elementos que otimizam o desempenho do molde durante a fabricação.
6. Testes de Moldes
Uma vez montado, o molde precisa passar por testes para verificar seu desempenho. Os testes incluem a realização de ciclos de produção em pequena escala, onde o molde é utilizado para fabricar algumas peças. Esse procedimento permite identificar quaisquer problemas, como falhas de montagem ou desajustes dimensionais.
Durante os testes, é crucial monitorar a qualidade das peças produzidas. Elas devem ser examinadas quanto a defeitos superficiais, dimensões e propriedades mecânicas. Se forem encontrados problemas, ajustes devem ser realizados no molde antes de prosseguir com a produção em larga escala.
7. Implementação de Melhorias
Com base nos resultados dos testes, pode ser necessário implementar melhorias no molde. Isso pode incluir ajustes nas dimensões, alterações na configuração ou modificações nos sistemas de resfriamento. O objetivo é maximizar a eficiência e a qualidade da produção.
Além disso, feedback da equipe de produção pode ser valioso nesse estágio, pois os operadores têm uma visão prática do desempenho do molde e podem oferecer sugestões baseadas na experiência. A colaboração entre as equipes de design, engenharia e produção é fundamental para otimizar o molde.
8. Produção em Larga Escala
Após a validação dos testes e a implementação das melhorias necessárias, o molde está pronto para a produção em larga escala. Neste estágio, o molde será utilizado em uma linha de produção, onde pode gerar centenas ou milhares de peças, dependendo da demanda.
É essencial manter um controle de qualidade rigoroso durante a produção em larga escala, realizando inspeções frequentes nas peças fabricadas. Essas inspeções ajudam a identificar rapidamente quaisquer variações de qualidade, permitindo que correções sejam feitas naturalmente.
9. Manutenção do Molde
A manutenção regular do molde é vital para garantir sua durabilidade e desempenho ao longo do tempo. Oito componentes do molde devem ser inspecionados, limpos e reparados conforme necessário, garantindo um bom funcionamento e evitando falhas.
A frequência da manutenção pode variar com base na intensidade do uso do molde e no tipo de material que ele processa. Moldes que operam com materiais abrasivos ou em temperaturas extremas podem exigir manutenção mais frequente para funcionar de maneira eficaz e prolongar sua vida útil.
10. Documentação e Registro
Por fim, a documentação de todo o processo de produção do molde é uma etapa importante que muitas vezes é negligenciada. É fundamental registrar todas as especificações, ajustes, testes realizados, e resultados obtidos para referência futura.
Esse conjunto de dados ajuda a equipe a compreender a história do molde e permite que melhorias sejam implementadas em futuras produções com facilidade. A documentação adequada também é útil em caso de auditorias ou certificações de qualidade.
Considerações Finais
O passo a passo na produção de moldes é um processo crítico que requer atenção a cada detalhe. Desde o planejamento e design até a manutenção e documentação, todas as etapas devem ser seguidas com cuidado para garantir a eficácia e a qualidade do produto final. Compreender cada fase não apenas melhora o conhecimento técnico, mas também contribui para a inovação e a eficiência dentro do setor industrial.
Investir em processos bem estruturados de produção de moldes resulta em produtos de alta qualidade, redução de custos e satisfação do cliente. À medida que a tecnologia avança e novas técnicas são introduzidas, a contínua atualização e adaptação às melhores práticas se torna essencial para manter a competitividade no mercado.
Dicas para Otimizar a Produção de Moldes
A produção de moldes é um processo complexo que demanda atenção a diversos detalhes para garantir eficiência e qualidade. Otimizar este processo pode resultar em redução de custos, melhoria na qualidade do produto final e aumento da produtividade. Neste artigo, apresentaremos dicas valiosas que podem ser adotadas para otimizar a produção de moldes, aprimorando cada etapa e garantindo resultados superiores.
1. Investir em Tecnologia de Ponta
Uma das maneiras mais efetivas de otimizar a produção de moldes é investir em tecnologias de ponta. Equipamentos modernos, como máquinas de usinagem de alta precisão e softwares CAD/CAM, podem aumentar significativamente a qualidade e a eficiência na fabricação de moldes. Essas tecnologias permitem a automação de muitos processos e garantem que as peças sejam produzidas com precisão milimétrica.
Além disso, a utilização de impressoras 3D para prototipagem rápida de moldes pode economizar tempo e recursos ao permitir a criação de modelos físicos antes da fabricação final. Isso facilita a visualização e o ajuste de design, reduzindo a probabilidade de erros futuros.
2. Treinamento da Equipe
O treinamento contínuo da equipe envolvida na produção de moldes é fundamental para garantir que todos estejam atualizados sobre as melhores práticas e novas tecnologias. Funcionários bem treinados podem identificar problemas rapidamente e propor soluções eficazes, resultando em menos erros e desperdícios.
Investir em workshops e cursos de capacitação não só melhora as habilidades técnicas da equipe, mas também os motiva a buscar inovações e melhorias no processo. Um time capacitado é um dos maiores ativos de uma empresa e, quando bem treinado, pode contribuir significativamente para a otimização da produção de moldes.
3. Análise e Melhoria de Processos
A análise contínua dos processos de produção é essencial para identificar gargalos e áreas que necessitam de melhorias. Métodos como o Six Sigma e Lean Manufacturing podem ser aplicados para mapear o fluxo de trabalho, detectar ineficiências e implementar melhorias.
Essas abordagens focam na eliminação de desperdícios e na maximização da eficiência, levando a uma produção mais ágil e econômica. Realizar revisões regulares nos processos de produção ajuda a manter o foco na melhoria contínua e no ajuste das metodologias de trabalho.
4. Controle de Qualidade Rigoroso
Um controle de qualidade rigoroso é vital para garantir que os moldes produzidos atendam às especificações esperadas. A implementação de sistemas de monitoramento e testes durante todo o processo de produção permite que problemas sejam detectados rapidamente e corrigidos antes que se tornem grandes falhas.
Manter um registro detalhado dos resultados de controle de qualidade ajuda a identificar tendências e padrões que podem ser abordados para melhorar a produção. A exemplo disso, se um tipo específico de molde estiver apresentando problemas de qualidade, será possível agir rapidamente para averiguar e corrigir as causas.
5. Planejamento Adequado da Produção
Um planejamento eficiente da produção é crucial para otimizar a fabricação de moldes. Isso inclui a definição de prazos realistas e a programação adequada dos recursos disponíveis, como mão de obra e matérias-primas. Um cronograma bem estruturado garantirá que as etapas do processo sejam seguidas de maneira fluida e que não ocorram atrasos significativos.
A utilização de ferramentas de planejamento e gerenciamento de projetos também pode facilitar a visualização do progresso e a identificação de possíveis atrasos. Mantendo um fluxo de trabalho organizado, as equipes podem colaborar mais eficazmente e manter a produtividade alta.
6. Seleção de Materiais de Alta Qualidade
A escolha dos materiais utilizados na fabricação de moldes é um fator crucial que impacta a qualidade e a durabilidade do produto final. Investir em materiais de alta qualidade pode reduzir manutenções frequentes e aumentar a vida útil do molde, resultando em menos paradas de produção e maior eficiência.
É importante considerar não apenas o custo dos materiais, mas também suas propriedades e como eles se comportarão durante o processo de fabricação. Optar por materiais adequados ao tipo de processo e às condições de operação selecionadas garante que os moldes resistam ao desgaste e consigam desempenhar suas funções de forma eficaz.
7. Colaboração com Fornecedores
Manter uma boa relação com os fornecedores de materiais e componentes é fundamental para garantir a qualidade e a pontualidade nas entregas. A colaboração próxima permite que as empresas tenham acesso a inovações e melhorias em produtos, ajudando a otimizar ainda mais a produção.
Além disso, uma comunicação clara com os fornecedores sobre demandas específicas e feedback em relação aos materiais entregues pode contribuir para um melhor entendimento entre ambas as partes, resultando em um processo de compra mais eficiente.
8. Implementação de Manutenção Preventiva
A manutenção preventiva é uma estratégia essencial para garantir que as máquinas e equipamentos utilizados na produção de moldes funcionem de maneira eficiente. Ao realizar manutenções programadas, é possível evitar quebras inesperadas e paradas de produção, resultando em maior eficiência e redução de custos operacionais.
Um cronograma de manutenção preventiva deve ser desenvolvido para garantir que todas as máquinas sejam verificadas regularmente. Investir na manutenção adequará a performance do maquinário e prolongará sua vida útil.
9. Uso de Simulações e Prototipagem
A utilização de simulações no design dos moldes e a realização de protótipos podem trazer grandes melhorias no processo de produção. Com simulações, é possível avaliar como o molde se comportará durante o processo de fabricação e identificar potenciais falhas antes de entrar em produção. Isso pode economizar tempo e recursos significativos, evitando alterações caras e demoradas.
A prototipagem também permite que os designers experimentem diferentes abordagens e designs, ajustando rapidamente as especificações conforme o feedback das equipes de produção e controle de qualidade.
10. Avaliação de Desempenho e Feedback
Finalmente, é fundamental realizar avaliações de desempenho regularmente e solicitar feedback de todos os envolvidos no processo de produção. As opiniões da equipe operativa e de controle de qualidade podem fornecer insights valiosos sobre áreas que necessitam de melhorias.
Além disso, criar uma cultura de feedback contínuo e aberto pode levar a inovações e ao aprimoramento dos processos. Reuniões regulares para discutir o desempenho da produção e possíveis melhorias ajudam a manter a equipe engajada e direcionada para a otimização.
Considerações Finais
Otimizar a produção de moldes é uma combinação de várias estratégias e práticas que visam melhorar a eficiência e a qualidade. Implementar as dicas apresentadas pode resultar não apenas na melhoria da linha de produção, mas também na satisfação do cliente através da entrega de produtos de alta qualidade.
A busca por inovação, eficiência e qualidade deve ser uma jornada contínua. À medida que a tecnologia avança e novas metodologias surgem, é essencial que as empresas se mantenham atualizadas e dispostas a adaptar suas práticas. Ao colocar em prática essas dicas, você estará não apenas otimizando a produção de moldes, mas também contribuindo para o crescimento e sucesso de sua organização.
Em conclusão, a produção de moldes é uma etapa vital que impacta diretamente a qualidade, eficiência e custo da fabricação de peças em diversas indústrias. Ao entender a importância dessa prática e os tipos de moldes disponíveis, as empresas podem tomar decisões informadas que otimizam seus processos produtivos. As dicas apresentadas para otimizar a produção de moldes, que vão desde a adoção de tecnologias modernas até a escolha de materiais adequados, são fundamentais para garantir não apenas a qualidade dos produtos, mas também para melhorar a competitividade no mercado. Ao investir em treinamento, colaboração e melhorias contínuas, sua empresa estará bem equipada para enfrentar os desafios do setor e, assim, alcançar resultados significativos. Portanto, ao aplicar essas estratégias, você não apenas expandirá suas capacidades de produção, mas também assegurará a satisfação dos clientes por meio de produtos finais de alta qualidade.