Fabricação de Moldes de Injeção: Guia Completo
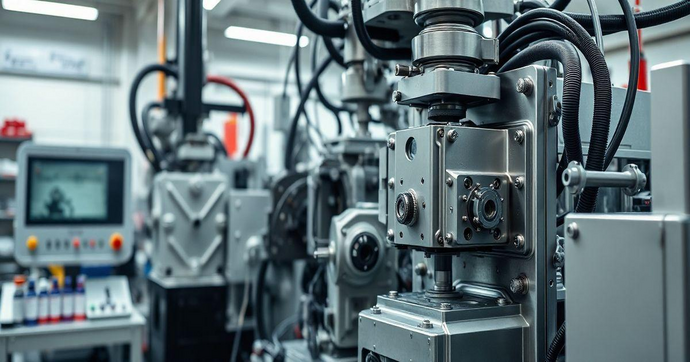
Por: Leonardo - 29 de Dezembro de 2024
A fabricação de moldes de injeção é uma etapa crucial na produção industrial, responsável pela criação de peças plásticas com alta precisão e eficiência. Neste artigo, vamos explorar o que são moldes de injeção, os diferentes tipos disponíveis e o processo envolvido em sua fabricação. Além disso, você aprenderá sobre os materiais utilizados, as vantagens deste método e as tendências atuais na indústria. Continue lendo e descubra como maximizar a qualidade e a eficiência na fabricação de moldes de injeção.
O que são moldes de injeção
Os moldes de injeção são ferramentas utilizadas no processo de injeção de plásticos, um método amplamente empregado na indústria para produzir peças e componentes de diversas formas e tamanhos. Este processo envolve a injeção de um material plástico fundido dentro de um molde, onde ele esfria e se solidifica, adquirindo a forma desejada. Assim, os moldes de injeção desempenham um papel fundamental na fabricação de produtos de plástico, permitindo a produção em grande escala com alta precisão e repetibilidade.
Os moldes são geralmente feitos de aço ou alumínio, com um design complexo que se adapta ao produto final que se deseja fabricar. A fabricação de moldes de injeção requer equipamentos sofisticados e um alto nível de especialização, considerando que o molde deve suportar altas pressões e temperaturas durante o processo de injeção. Por isso, é comum que essa atividade seja realizada por Empresas de injeção plástica, que possuem a experiência e os recursos necessários para garantir a qualidade dos moldes produzidos.
Os moldes de injeção são projetados de forma a maximizar a eficiência e minimizar o desperdício de material. O processo começa com a criação de um protótipo digital da peça a ser produzida, utilizando softwares de CAD (Desenho Assistido por Computador). Esta etapa é crucial, pois qualquer erro no design pode resultar em um molde que não funcione corretamente, levando a perdas de tempo e recursos.
Após a definição do projeto, inicia-se a fabricação do molde, que pode envolver processos como fresagem, usinagem e eletroerosão. Cada etapa é realizada com precisão, já que pequenos desvios podem impactar a qualidade da peça final. O molde é então montado e testado, para garantir que esteja livre de falhas e pronto para a produção.
Outro aspecto importante é o ciclo de injeção, que é o tempo que leva para injetar o plástico no molde, esfriá-lo e demorar o molde. Esse ciclo pode variar dependendo do tipo de plástico utilizado, da complexidade da peça e da eficiência da máquina injetora. O controle rigoroso do ciclo de injeção é essencial para garantir a qualidade das peças, evitando defeitos como bolhas, distorções ou quebras.
Além de serem utilizados na fabricação de itens de uso cotidiano, como embalagens, brinquedos, peças automotivas e produtos eletrônicos, os moldes de injeção também são aplicados em segmentos específicos, como o médico e o de embalagens industriais. A versatilidade dos moldes permite que sejam criados designs personalizados que atendam às necessidades específicas de cada cliente ou mercado.
Os moldes de injeção podem ser classificados em diferentes tipos, como moldes de injeção de um ou múltiplos cavidades, moldes de injeção quente e frios, cada um apresentando suas vantagens e desvantagens. Moldes de injeção de múltiplas cavidades, por exemplo, são projetados para produzir várias peças em um único ciclo, aumentando a eficiência da produção, mas também exigindo um investimento maior e um design mais complexo.
A evolução das tecnologias de fabricação também trouxe inovações para a produção de moldes de injeção. Métodos como a impressão 3D estão começando a ser utilizados para criar moldes de protótipos mais rapidamente, permitindo que designers testem e aprimorem seus projetos antes da fabricação em larga escala. Isso não apenas reduz o tempo de desenvolvimento, mas também facilita a personalização e a modificação de moldes para atender às demandas do mercado.
Além disso, a sustentabilidade está se tornando uma preocupação cada vez mais presente na indústria. Muitas empresas estão buscando maneiras de reduzir o desperdício de plástico e melhorar a eficiência energética durante o processo de injeção. As inovações incluem a utilização de plásticos recicláveis e biocompatíveis, bem como a implementação de processos de recuperação de temperatura que podem economizar energia e reduzir os custos operacionais.
Em resumo, os moldes de injeção são uma parte vital da indústria de fabricação, permitindo a produção eficiente e precisa de uma vasta gama de produtos plásticos. A compreensão desse processo é fundamental para empresas que buscam otimizar sua produção e se manter competitivas no mercado. Seja pela utilização de tecnologias avançadas ou pela escolha de materiais sustentáveis, o futuro da fabricação de moldes de injeção parece promissor e cheio de inovações.
Tipos de moldes de injeção
Existem diversos tipos de moldes de injeção, cada um projetado para atender a necessidades específicas de produção e características do produto final. Essa diversidade é fundamental para garantir que as peças plásticas sejam produzidas com eficiência, qualidade e precisão. Abaixo, veremos os principais tipos de moldes de injeção utilizados na indústria, seus funcionamentos e aplicações, oferecendo uma visão abrangente sobre esse tema tão relevante.
Um dos tipos mais comuns de moldes de injeção é o molde de cavidade única. Como seu nome sugere, esse molde possui apenas uma cavidade, ou seja, produz uma peça por ciclo de injeção. Embora esse tipo de molde possa ser mais simples e, geralmente, mais barato, sua eficiência pode ser limitada, especialmente em operações de alta produção. Muitos fabricantes optam por moldes de cavidade única quando a demanda por peças não é tão elevada ou quando a complexidade da peça justifica a qualidade que um molde mais elaborado pode oferecer.
Em contrapartida, os moldes de múltiplas cavidades são projetados para produzir várias peças em um único ciclo. Esses moldes possuem várias cavidades, permitindo que um maior número de produtos seja fabricado ao mesmo tempo. Embora exibam um investimento inicial mais alto, sua eficiência e a redução nos custos de produção em grandes escalas podem compensar esses gastos. Este tipo de molde é amplamente utilizado em indústrias que requerem grande volume de produção, como a fabricação de brinquedos, peças automotivas e embalagens.
Outro tipo importante de molde é o molde de injeção quente, que utiliza um sistema de aquecimento para manter o material plástico em estado fundido até que seja injetado no molde. Essa técnica diminui o tempo de resfriamento e pode resultar em uma melhor qualidade da peça, já que o plastificante tem mais tempo para preencher a cavidade. Moldes de injeção quente são ideais para produtos que exigem alta complexidade e detalhamento finos, permitindo um fluxo de material mais uniforme e evitando problemas como a formação de bolhas de ar.
Os moldes de injeção frios possuem um sistema de resfriamento que inicia o processo de solidificação imediatamente após a injeção. Este método é mais simples e amplamente utilizado, principalmente para peças de geometria mais simples, onde a velocidade de produção é prioritária em relação à complexidade do design do componente.
Além disso, existe a categoria de moldes de injeção de baixo e alto impacto. Os moldes de baixo impacto são frequentemente utilizados para produções em massa onde a taxa de defeitos precisa ser minimizada, enquanto os moldes de alto impacto são usados para produtos que precisarão suportar forças significativas, tornando-se uma escolha comum em peças que farão parte de produtos eletrônicos ou automotivos.
Os moldes de injeção com núcleo e cavidade são mais sofisticados e incluem características de design que permitem a produção de peças mais complexas com geometrias intrincadas. Eles são projetados de forma a permitir a inserção de componentes durante o processo de fabricação, sendo muito utilizados na produção de peças com recursos adicionais, como furos ou fendas.
Outro tipo é o molde de injeção de dupla injeção, ideal para a fabricação de peças feitas de dois materiais diferentes, que podem ser injetados sequencialmente ou simultaneamente, resultando em produtos com características diferentes, como texturas ou colorações. Esse tipo de molde traz um desafio adicional aos engenheiros de design e fabricação, mas em troca oferece produtos mais inovadores e versáteis.
Além das categorias acima, é importante mencionar que a Ferramentaria de moldes plasticos oferece a possibilidade de personalizar os moldes de acordo com as necessidades específicas do cliente. O uso de tecnologias como impressão 3D e softwares avançados de design facilita a criação de moldes únicos, otimizando a produção em função das demandas do mercado.
Por fim, para determinar qual tipo de molde de injeção é o mais adequado para um projeto específico, é necessário considerar fatores como o volume de produção, a complexidade da peça, os materiais a serem utilizados e o orçamento disponível. Uma escolha adequada pode significar a diferença entre um produto de sucesso e uma produção ineficiente, resultando em desperdício de recursos e custos altos.
Para concluir, entender os diferentes tipos de moldes de injeção é essencial para indústrias que buscam eficiência, qualidade e inovação. Na era da produção em massa, a escolha do tipo de molde ideal pode melhorar significativamente a competitividade e a versatilidade das empresas no mercado global.
Processo de fabricação de moldes de injeção
O processo de fabricação de moldes de injeção é uma operação complexa que envolve várias etapas críticas, desde o design até a produção final. Esse processo é fundamental para garantir que os moldes atendam a todas as especificações e requisitos necessários para a produção de peças plásticas de alta qualidade. A seguir, detalharemos as etapas principais do processo de fabricação de moldes de injeção, destacando a importância da Ferramentaria e usinagem neste contexto.
A primeira fase do processo de fabricação é o desenvolvimento do design do molde. Essa etapa começa com a criação de um modelo 3D da peça que se deseja produzir, utilizando software de CAD (Desenho Assistido por Computador). É crucial que os engenheiros e projetistas considerem não apenas a forma e as dimensões da peça, mas também fatores como as propriedades do material, as características de injeção e a viabilidade da produção. O design do molde deve levar em conta detalhes técnicos, como a distribuição do fluxo do plástico, sistemas de resfriamento e os pontos de injeção.
Após a finalização do projeto, a próxima etapa consiste na fabricação do molde propriamente dito. Esta fase envolve uma série de processos de usinagem, que podem incluir fresagem, torneamento, eletroerosão e furação. A escolha das ferramentas e técnicas de usinagem adequadas é essencial, pois elas vão influenciar a precisão e a qualidade da peça final. As máquinas utilizadas devem ser de alta precisão, uma vez que pequenos desvios podem resultar em falhas no molde, comprometendo a produção das peças.
Durante a fresagem, o material do molde é removido para criar a forma desejada. Este é frequentemente um dos processos mais longos, pois requer atenção aos detalhes e a utilização de diversas ferramentas para garantir que todas as características do design sejam respeitadas. Uma vez que a estrutura básica do molde está pronta, a próxima etapa é a eletroerosão, que permite a criação de formas complicadas e detalhes finos. Esse processo é particularmente útil, uma vez que moldes com geometrias complexas podem ser muito desafiadores de se produzir com técnicas de usinagem tradicionais.
Após a usinagem, as superfícies do molde precisam ser tratadas e polidas. Esta fase é crucial, pois superfícies rugosas podem afetar a qualidade da peça final, causando imperfeições visíveis. O polimento adequado também ajuda a garantir que o plástico possa ser facilmente removido do molde após o processo de injeção, minimizando o risco de danos. Existem diversas técnicas de polimento, desde o uso de lixas e polidores manuais até processos automatizados com equipamentos especializados.
Depois que o molde é fabricado e tratado, ele passa por uma fase de montagem, onde todas as partes do molde são unidas em um sistema completo. Esta fase muitas vezes inclui a instalação de componentes adicionais, como sistemas de resfriamento e mecanismos de liberação, que são essenciais para o bom funcionamento do molde durante a injeção. O ajuste fino dessas partes é fundamental para garantir que o molde funcionará como previsto durante a produção.
Uma vez montado, o molde é submetido a testes de funcionamento para verificar se ele atende a todos os requisitos de produção. Esses testes são realizados com materiais de injeção e têm como objetivo identificar quaisquer problemas antes da produção em larga escala. Durante esta fase, o molde poderá ser ajustado e otimizado, se necessário, garantindo que não haja falhas que possam afetar a eficiência da produção ou a qualidade das peças.
Após a conclusão dos testes e ajustes finais, o molde está pronto para ser colocado em uma máquina de injeção. A produção em larga escala pode então começar, utilizando o molde para criar as peças projetadas. Durante essa fase, o desempenho do molde é monitorado para garantir que ele continue funcionando conforme esperado ao longo de todo o ciclo de produção. O controle da qualidade continua sendo uma parte crucial do processo, pois peças defeituosas podem resultar em desperdício de material e tempo.
Finalmente, é importante notar que o processo de fabricação de moldes de injeção não termina com a produção de um único molde. A manutenção regular e a inspeção contínua são essenciais para garantir a longevidade e a eficiência do molde. Com o uso frequente, os moldes podem sofrer desgaste e exigir reparos ou substituições de componentes. Assim, uma gestão adequada da manutenção prolonga a vida útil dos moldes e garante a continuidade da produção sem interrupções.
Em resumo, o processo de fabricação de moldes de injeção é uma operação complexa que envolve várias etapas importantes, desde o design inicial até a produção final. A precisão em cada uma dessas fases é fundamental para garantir que os moldes sejam eficientes e produzam peças de alta qualidade. Com a evolução das tecnologias de usinagem e design, a fabricação de moldes se torna cada vez mais sofisticada, permitindo inovações e melhorias contínuas na produção. Ao entender cada etapa desse processo, as empresas podem se preparar melhor para atender às demandas do mercado e se manter competitivas.
Materiais utilizados na fabricação de moldes
A fabricação de moldes de injeção é uma etapa crítica na produção de peças plásticas, e a escolha dos materiais utilizados nesse processo é fundamental para garantir a qualidade e a durabilidade dos moldes. Diversos fatores devem ser considerados na seleção de materiais, incluindo a complexidade do design do molde, o tipo de plástico a ser injetado e os requisitos de produção em termos de volume e frequência. A seguir, exploraremos os materiais mais comuns utilizados na fabricação de moldes de injeção.
Um dos materiais mais utilizados para a fabricação de moldes de injeção é o aço. O aço oferece uma combinação ideal de resistência, durabilidade e resistência ao desgaste, tornando-o uma escolha preferencial para muitos fabricantes. Existem diferentes tipos de aços que podem ser utilizados, sendo os mais comuns o aço carbono e o aço ferramenta. O aço ferramenta, em particular, é tratado termicamente para obter propriedades específicas, como maior dureza e resistência ao impacto, o que é essencial para moldes que serão utilizados repetidamente em ambientes de produção intensa.
O aço inoxidável é outra opção, conhecido por sua resistência à corrosão. Este material é especialmente útil para moldes que trabalharão com materiais plásticos que podem ser abrasivos ou que requerem um tratamento mais rigoroso. Moldes feitos de aço inoxidável são ideais para aplicações em indústrias alimentícias e farmacêuticas, onde a contaminação deve ser evitada a todo custo.
Além do aço, a liga de alumínio também é um material popular na fabricação de moldes de injeção. O alumínio é mais leve que o aço, o que pode resultar em tempos de ciclo mais curtos e uma redução nos custos de energia durante o processo de produção. A leveza do alumínio também facilita a manipulação e instalação do molde, tornando-o uma opção atraente para a produção de protótipos ou pequenas séries. No entanto, os moldes de alumínio podem não ser tão duráveis quanto os de aço, e geralmente são mais adequados para produções de baixo a médio volume.
Os plásticos de engenharia, como o POM (Poliacetal) e o nylon, também encontram aplicação em moldes de injeção, especialmente em situações onde a resistência ao impacto e à abrasão são exigidas. Esses materiais podem ser utilizados em moldes de injeção para produtos de consumo ou componentes de uso industrial, onde a combinação das propriedades dos plásticos e a eficiência no processo de injeção de plastico podem resultar em produtos de alta qualidade.
Outro material em ascensão na fabricação de moldes de Injeção de plastico é a impressão 3D, que permite criar moldes a partir de polímeros, resinas e metais. A impressão 3D oferece uma flexibilidade no design que é difícil de alcançar com métodos tradicionais, permitindo a produção de moldes personalizados com geometrias complexas. Essa tecnologia é particularmente útil para protótipos rápidos e para a criação de moldes para peças de baixa tiragem, onde o custo de um molde tradicional pode não ser viável.
Além dos materiais utilizados na fabricação dos moldes, a escolha do revestimento é igualmente importante. Alguns moldes são revestidos com materiais especiais, como nitreto ou cromado, para reduzir o desgaste e aumentar a resistência à corrosão. Os revestimentos ajudam a prolongar a vida útil do molde e melhoram o desempenho durante o ciclo de injeção, especialmente em aplicações que envolvem materiais abrasivos.
A temperatura de operação é outro fator que deve ser considerado ao escolher os materiais para a fabricação de moldes. Os materiais devem ser capazes de suportar as altas temperaturas que ocorrem durante o processo de injeção. Um tratamento térmico adequado pode aumentar a resistência do material e permitir que ele suporte pressões extremas, sem apresentar deformações ou falhas.
Por fim, a escolha dos materiais para a fabricação de moldes de injeção determina não apenas a eficiência do processo, mas também a qualidade da peça final produzida. Um molde bem projetado e construído, utilizando materiais adequados, pode resultar em economia significativa de tempo e recursos ao longo do ciclo de produção, minimizando desperdícios e melhorando a produtividade geral.
Em resumo, os materiais utilizados na fabricação de moldes de injeção variam amplamente, cada um com suas características e propriedades específicas que os tornam adequados para diferentes aplicações. A escolha do material apropriado é uma decisão crítica que impacta diretamente na qualidade do molde e, por sua vez, no processo de produção de peças de plástico. Com a evolução das tecnologias e a introdução de novos materiais, o futuro da fabricação de moldes parece promissor, permitindo aos fabricantes inovar e melhorar continuamente suas operações.
Vantagens da fabricação de moldes de injeção
A fabricação de moldes de injeção é um processo amplamente utilizado na indústria de produção de peças plásticas devido às inúmeras vantagens que oferece. Este método de produção não apenas fornece eficiência e precisão, mas também proporciona uma série de benefícios que o tornaram a escolha favorita para muitas empresas. Neste artigo, exploraremos as principais vantagens da fabricação de moldes de injeção.
Uma das principais vantagens da fabricação de moldes de injeção é a capacidade de produzir grandes volumes de peças de forma rápida e eficiente. Uma vez que o molde é fabricado e testado, ele pode ser usado repetidamente para produzir milhares, se não milhões, de unidades idênticas. Isso resulta em uma significativa redução do tempo de ciclo e custos de produção em comparação com outros métodos de manufatura, como a moldagem por sopro ou a conformação. Com a demanda crescente por produtos plásticos e a necessidade de produção em massa, essa eficiência torna-se um fator crucial para o sucesso das empresas.
Além disso, a precisão e a consistência das peças produzidas são outra grande vantagem. Os moldes de injeção são projetados com rigor e podem alcançar tolerâncias muito estreitas. Isso significa que cada peça produzida terá dimensões exatas, evitando a variabilidade que pode ocorrer em outros processos de fabricação. A alta precisão é especialmente importante em indústrias como a automotiva e a eletrônica, onde a qualidade e o desempenho dos componentes são críticos.
Outro ponto a favor da moldagem por injeção é a flexibilidade em termos de design e formatos. Com os moldes de injeção, é possível criar peças complexas com geometrias intrincadas que podem ser difíceis ou impossíveis de obter com outros métodos. O design dos moldes pode ser adaptado para incluir características específicas, como fendas, texturas ou partes móveis, aumentando a versatilidade dos produtos finais. Essa capacidade de inovação é essencial para atender às demandas variadas dos consumidores e se destacar em um mercado competitivo.
A fabricação de moldes de injeção também oferece uma excelente oportunidade para reduzir o desperdício de materiais. No processo de injeção, o plástico é moldado diretamente na forma desejada, minimizando a necessidade de retrabalho e corte excessivo, que são comuns em outros processos. Isso não só economiza recursos, mas também contribui para práticas de produção mais sustentáveis. Em um mundo onde a sustentabilidade é cada vez mais valorizada, essa característica pode ser um diferencial importante para as empresas.
O material utilizado na fabricação de moldes de injeção, geralmente aço ou alumínio, confere ainda mais vantagens. Esses materiais são altamente duráveis e resistentes ao desgaste, o que resulta em uma vida útil prolongada dos moldes. Além disso, a possibilidade de tratamento e revestimento dos materiais aumenta ainda mais a resistência dos moldes, permitindo que eles suportem altas pressões e temperaturas sem comprometer a qualidade das peças. Esta durabilidade é especialmente útil em ambientes de produção de alta intensidade, onde os moldes são utilizados continuamente.
Outro benefício relevante da fabricação de moldes de injeção é a economia de tempo em comparação com outros métodos de produção. Uma vez que o processo de design e fabricação do molde é completado, as peças podem ser produzidas em um ciclo de produção rápida. Em muitas situações, os prazos de entrega podem ser significativamente reduzidos, permitindo que as empresas respondam rapidamente à demanda do mercado. Isso é especialmente crucial em setores onde a agilidade é essencial para manter a competitividade.
A capacidade de realizar testes antes da produção em massa também é uma vantagem significativa. Com moldes de injeção, é possível realizar um protótipo inicial e testar o desempenho da peça antes de entrar em produção em larga escala. Isso permite que as empresas identifiquem e solucionem quaisquer problemas de design ou funcionalidade previamente, economizando tempo e dinheiro a longo prazo. A validação do design é um passo fundamental para garantir a qualidade e a confiabilidade dos produtos finais.
Finalmente, os custos de produção a longo prazo tendem a ser mais baixos com a fabricação de moldes de injeção. Embora o investimento inicial na fabricação do molde possa ser elevado, os custos por unidade diminuem significativamente com o aumento da produção. Além disso, a redução do desperdício de materiais e a minimização de retrabalho contribuem para a viabilidade financeira do processo. As empresas podem, portanto, maximizar sua margem de lucro enquanto garantem a qualidade dos produtos.
Em resumo, as vantagens da fabricação de moldes de injeção são muitas e variadas. A capacidade de produzir grandes volumes de peças com alta precisão, a flexibilidade em design e a diminuição do desperdício são apenas algumas das razões pelas quais esse método é popular na indústria. Para empresas que buscam eficiência, qualidade e sustentabilidade, a fabricação de moldes de injeção representa uma escolha estratégica que pode levar ao sucesso a longo prazo no competitivo mercado de produção de plásticos.
Manutenção de moldes de injeção
A manutenção de moldes de injeção é uma parte crucial do processo de fabricação de peças plásticas, uma vez que moldes bem cuidados garantem a eficiência, a qualidade e a durabilidade da produção. Moldes de injeção são ferramentas complexas que estão sujeitas a desgaste e danificações devido ao uso contínuo, altas pressões e temperaturas envolvidas durante o processo de injeção. Portanto, uma estratégia de manutenção eficaz é essencial para maximizar a vida útil dos moldes e minimizar custos operacionais. Neste artigo, discutiremos a importância da manutenção de moldes de injeção e forneceremos dicas práticas para os fabricantes.
Uma das principais razões para realizar a manutenção regular é que moldes mal conservados podem levar a problemas sérios na produção. O desgaste nas superfícies do molde, como arranhões ou desgastes, pode causar defeitos nas peças produzidas, resultando em desperdício de material e tempo. Problemas como empenamentos, quebras ou dificuldades na desmoldagem também podem ocorrer, interferindo no fluxo de produção. A manutenção preventiva ajuda a identificar esses problemas antes que se tornem críticos, garantindo que a produção continue de maneira eficiente.
A manutenção preventiva deve ser programada regularmente, incluindo inspeções visuais e funcionais dos moldes. Verificar se há sinais de desgaste, corrosão ou danos é uma tarefa essencial para manter a qualidade dos moldes. É recomendado que essas inspeções sejam feitas após cada ciclo de produção ou ainda em intervalos regulares, dependendo da intensidade do uso do molde. Durante essas inspeções, um técnico especializado deve observar as superfícies de contato, os sistemas de resfriamento e a estrutura geral do molde.
Outro aspecto importante da manutenção de moldes de injeção é a limpeza adequada. Resíduos de plástico, sujeira e outros contaminantes podem se acumular nas cavidades do molde, afetando o fluxo do material e a qualidade das peças.fabricadas. Para evitar esses problemas, é essencial aplicar um detergente adequado, seguido de enxágue e secagem, garantindo que todas as superfícies estejam livres de contaminantes. Além disso, algumas empresas utilizam soluções de ultrassom para limpar moldes de injeção, especialmente aqueles que têm geometrias complexas e detalhes intrincados.
Além da limpeza regular, a lubrificação dos moldes também é um aspecto fundamental da manutenção. A falta de lubrificação pode levar ao aumento do atrito e do desgaste nas superfícies do molde, resultando em um encurtamento de sua vida útil. As partes móveis, como puxadores e mecanismos de liberacão, devem ser lubrificadas constantemente com óleos ou graxas apropriados, garantindo que funcionem adequadamente. Uma lubrificação correta minimiza o desgaste e permite que os moldes operem suavemente durante o uso.
Além dos cuidados preventivos, a manutenção corretiva deve ser realizada sempre que um problema for identificado. Isso pode incluir o reparo de superfícies danificadas, a troca de componentes desgastados ou até mesmo a re-doresagem de algumas áreas do molde. É fundamental que esses reparos sejam realizados rapidamente para evitar que pequenos problemas se transformem em questões mais graves, que podem exigir intervenções mais complexas e custosas. Em certos casos, moldes que foram severamente danificados podem precisar ser reencontrados, o que pode resultar em perdas significativas para a produção.
A documentação adequada é outro ponto importante na manutenção de moldes de injeção. Manter registros detalhados das inspeções, limpezas e reparos realizados em cada molde permite que a equipe de manutenção tenha uma visão clara do histórico do molde. Isso não apenas ajuda a programar as intervenções necessárias, mas também permite identificar padrões e melhorar os processos de manutenção. Com um bom controle da documentação, a manutenção se torna mais eficiente e eficaz, aumentando o desempenho e a durabilidade dos moldes.
Um programa de treinamento adequado para os operadores e equipe de manutenção também é essencial para a eficácia na manutenção dos moldes. Garantir que os funcionários estejam bem treinados nas melhores práticas de manuseio e manutenção pode reduzir o risco de danos acidentais e garantir que os moldes sejam tratados com o cuidado necessário. Treinamentos regulares sobre o uso de equipamentos, cuidados com os moldes e técnicas de limpeza são fundamentais para o sucesso do programa de manutenção.
Por fim, é importante mencionar que a manutenção de moldes de injeção não é apenas uma questão de preservação de ativos, mas também de otimização da produção. Moldes bem mantidos resultam em uma maior eficiência na fabricação, com menos interrupções e menos retrabalho. Isso leva a uma redução significativa dos custos operacionais e um aumento da capacidade produtiva da empresa. Em última análise, investir em programas de manutenção de moldes de injeção é uma decisão estratégica que contribui para a competitividade e o sucesso a longo prazo de qualquer negócio no setor.
Em suma, a manutenção de moldes de injeção é uma prática essencial que não deve ser negligenciada. Com uma abordagem proativa e sistemática, as empresas podem maximizar a vida útil dos seus moldes, reduzir custos e garantir a qualidade dos produtos fabricados. A implementação de um programa sólido de manutenção pode fazer toda a diferença na eficiência da produção e no retorno sobre o investimento.
Erros comuns na fabricação de moldes
A fabricação de moldes de injeção é um processo que exige precisão e atenção aos detalhes para garantir a qualidade das peças produzidas. No entanto, mesmo os profissionais mais experientes podem cometer erros durante este processo complexo. Esses erros podem levar a desperdícios de materiais, aumento de custos e atrasos na produção. Neste artigo, discutiremos os erros mais comuns na fabricação de moldes, destacando como evitá-los para otimizar a eficiência e melhorar a qualidade dos produtos finais.
Um dos erros mais frequentemente encontrados na fabricação de moldes é a inadequada definição do design do molde. O design deve ser meticulosamente elaborado para acomodar todas as características e especificações do produto final. Quando um molde é projetado sem considerar fatores como o fluxo do material, as pressões de injeção e as condições de resfriamento, pode resultar em falhas na peça final, como deformações ou falhas estruturais. Para evitar esse erro, é crucial realizar análises detalhadas e simulações de fluxo de plástico durante a fase de design, utilizando softwares de CAD e CAE (análise assistida por computador).
Outro erro comum é a escolha inadequada dos materiais do molde. O material utilizado deve ser selecionado em função das propriedades do plástico a ser injetado e das condições de operação do molde. Por exemplo, um molde que trabalhará com plásticos abrasivos deve ser fabricado com um material resistente ao desgaste. Se um material inadequado for escolhido, pode resultar em desintegração prematura do molde e a necessidade de reparos ou substituições frequentes, aumentando exponencialmente os custos do projeto. Portanto, a seleção correta de materiais, levando em consideração as especificidades da aplicação, é essencial.
A falta de manutenção regular dos moldes também é um erro que pode causar sérios problemas. Moldes que não são devidamente mantidos podem acumular sujeira e resíduos, afetando sua funcionalidade e a qualidade das peças produzidas. Além disso, componentes desgastados ou danificados podem resultar em quebras ou falhas de produção. A implementação de um cronograma de manutenção preventiva, incluindo inspeções e limpezas regulares, pode ajudar a evitar esses problemas e prolongar a vida útil dos moldes.
Outro erro que não pode ser ignorado é a falta de testes e validações adequadas antes da produção em massa. Após a fabricação do molde, é importante realizar testes com amostras do produto final para identificar e corrigir possíveis falhas no design ou no funcionamento do molde. Ignorar esta etapa pode resultar em grandes defeitos nas peças produzidas, causando retrabalho e desperdício. Realizar testes de injeção com diferentes parâmetros, incluindo temperaturas e pressões, é fundamental para garantir que o molde funcione conforme esperado.
O gerenciamento inadequado dos prazos e da produção também é um erro que pode impactar negativamente a fabricação de moldes. A pressa na produção muitas vezes leva a cortes em processos fundamentais, como revisões de design e testes de qualidade. Essa abordagem pode resultar em moldes que não possuem a qualidade esperada, prejudicando a produção. Portanto, é essencial que as empresas estabeleçam prazos realistas e permitam tempo suficiente para cada etapa do processo de fabricação, garantindo que o controle de qualidade não seja comprometido.
Além disso, a comunicação deficiente entre as equipes envolvidas no projeto e na fabricação do molde pode gerar erros significativos. Se as informações não forem compartilhadas de maneira clara e eficaz, mal-entendidos podem surgir, levando a decisões erradas durante o processo de fabricação. Implementar um sistema de comunicação eficiente e reuniões regulares entre as equipes de design, engenharia e produção pode facilitar a troca de informações e reduzir a probabilidade de erros.
A utilização inadequada das ferramentas e máquinas durante a fabricação dos moldes também deve ser considerada. Cada equipamento possui especificações e limites de operação, e não respeitar essas diretrizes pode resultar em falhas na fabricação. O treinamento adequado para operadores e funcionários é essencial para garantir que eles conheçam as melhores práticas de uso dos equipamentos e entendam a importância de seguir os procedimentos recomendados.
Além disso, erros na programação das máquinas de injeção podem causar uma série de problemas, desde a injeção excessiva de material até a geração de bolhas ou outras imperfeições nas peças. Garantir que a programação seja realizada por profissionais qualificados e realizar ajustes constantes durante a produção pode ajudar a minimizar esses riscos. Consultar especialistas e utilizar tecnologia de monitoramento em tempo real durante a produção também pode ser benéfico.
Por fim, a falta de documentação adequada durante o processo de fabricação de moldes pode resultar em dificuldades na identificação de problemas e na busca por melhorias. Manter registros detalhados de cada passo do processo, desde o design até a produção e manutenção dos moldes, é essencial para permitir uma análise posterior e facilitar a identificação de falhas e oportunidades de aprimoramento. A documentação também serve como base para futuros projetos, garantindo que lições aprendidas não sejam esquecidas.
Em resumo, a fabricação de moldes de injeção envolve uma série de etapas que necessitam de atenção meticulosa para evitar erros comuns que podem impactar a produção. Os erros relacionados ao design do molde, escolha inadequada de materiais, manutenção insuficiente, falhas na validação, gestão ineficaz de prazos, comunicação deficiente, utilização incorreta de ferramentas e falta de documentação são apenas algumas das armadilhas que podem ser evitadas. Ao implementar práticas sólidas e prestar atenção a esses detalhes, as empresas podem melhorar a eficiência da produção e a qualidade dos produtos finalizados.
Tendências na indústria de moldes de injeção
A indústria de moldes de injeção está em constante evolução, impulsionada por inovações tecnológicas, demandas de mercado e a crescente necessidade de práticas sustentáveis. À medida que as empresas buscam maneiras de otimizar sua produção e atender às necessidades dos consumidores, várias tendências emergem nesse setor. Neste artigo, vamos explorar as principais tendências na indústria de moldes de injeção e como elas estão moldando o futuro da fabricação de peças plásticas.
Uma das principais tendências que têm impactado a indústria de moldes de injeção é a adoção de tecnologias de impressão 3D. A impressão 3D permite a criação de moldes mais complexos e personalizados em um tempo reduzido, além de oferecer uma flexibilidade que não é possível com os métodos tradicionais de fabricação. Essa tecnologia permite a produção rápida de protótipos, possibilitando a validação do design antes da fabricação do molde final. Isso não somente acelera o processo de desenvolvimento de produtos, mas também reduz o desperdício de material, tornando a fabricação mais eficiente e sustentável.
Outra tendência significativa é a automação e a digitalização dos processos de fabricação. A Indústria 4.0 está transformando a maneira como os moldes são projetados, fabricados e geridos. A integração de tecnologias como IoT (Internet das Coisas), inteligência artificial e análise de big data está permitindo que empresas monitorem continuamente o desempenho de seus moldes e máquinas. Essa abordagem proativa permite a identificação de problemas antes que se tornem críticos, otimizando o processo de produção e reduzindo o tempo de inatividade. À medida que mais empresas implementam esses sistemas, a eficiência operacional e a qualidade da produção aumentam.
Além disso, a sustentabilidade se tornou uma preocupação central na produção de moldes de injeção. Com a pressão crescente de consumidores e órgãos reguladores para a redução do impacto ambiental, as empresas estão buscando maneiras de tornar seus processos mais sustentáveis. Isso inclui a adoção de materiais recicláveis e biodegradáveis no processo de injeção, bem como a implementação de práticas de economia circular. A criação de moldes que utilizam plásticos reciclados não apenas reduz o desperdício, mas também atende à demanda por produtos mais ecológicos. A implementação de sistemas de gestão de resíduos e a otimização do consumo de energia também são tendências que estão se tornando padrão na indústria.
A personalização em massa também está ganhando destaque na fabricação de moldes de injeção. À medida que os consumidores se tornam mais exigentes e as demandas por produtos personalizados aumentam, as empresas precisam se adaptar a essas expectativas. Os moldes de injeção estão sendo projetados para acomodar pequenas alterações no design e na funcionalidade, permitindo a fabricação eficiente de produtos personalizados sem comprometer a produtividade. Essa tendência não só aumenta a satisfação do cliente, mas também permite que as empresas se destaquem em um mercado cada vez mais competitivo.
Outro aspecto relevante é a utilização de simuladores de fluxos de plástico. As ferramentas de simulação de moldagem são cada vez mais utilizadas durante a fase de design do molde, permitindo que os engenheiros testemunhem como o plástico fluirá dentro do molde antes da produção. Isso ajuda a identificar e corrigir potenciais problemas antes mesmo que o molde seja produzido, economizando tempo e recursos. Essa abordagem é especialmente valiosa para moldes complexos, onde um ajuste na dinâmica de fluxo pode fazer uma grande diferença na qualidade do produto final.
A especialização no design de moldes também é uma tendência crescente. Com a diversificação das aplicações e a complexidade dos produtos, há uma demanda crescente por moldes adaptados a necessidades específicas de indústrias, como automotiva, eletrônica, médica e de embalagens. Designers e engenheiros estão cada vez mais se especializando em nichos específicos, proporcionando soluções mais eficazes e inovadoras para as necessidades de cada setor. Isso resulta em moldes mais eficientes, que geram produtos finais com qualidade superior.
A tecnologia de monitoramento em tempo real está se tornando uma prática comum na indústria de moldes de injeção. Sistemas de monitoramento equipados com sensores são instalados em máquinas e moldes, permitindo que os operadores acompanhem o desempenho em tempo real. Isso possibilita a correção imediata de falhas e a otimização de processos, garantindo uma produção mais estável. O monitoramento em tempo real também oferece dados valiosos que podem ser analisados para futuras melhorias no processo de fabricação.
Finalmente, a colaboração entre fabricantes de moldes e empresas de injeção plástica está se tornando uma escolha estratégica na indústria. Essa parceria permite um entendimento profundo das necessidades específicas de cada cliente e facilita o desenvolvimento de soluções personalizadas. Além disso, essa colaboração resulta em um processo mais integrado, onde ambas as partes trabalham juntas para otimizar a produção e a qualidade dos produtos finais.
Em resumo, as tendências na indústria de moldes de injeção estão moldando um futuro mais inovador e sustentável para a fabricação de peças plásticas. A adoção de tecnologias como impressão 3D, automação, uso de materiais sustentáveis e simulação de processos está facilitateando a criação de moldes mais eficientes e adaptados às necessidades do mercado. À medida que a indústria avança, as empresas que abraçam essas tendências estarão melhor posicionadas para atender às demandas crescentes dos consumidores e melhorar sua competitividade no mercado global.
Em síntese, a fabricação de moldes de injeção é um elemento essencial na indústria, que desempenha um papel vital na criação de peças plásticas com elevado padrão de qualidade e eficiência. Ao longo deste artigo, exploramos as diversas facetas deste processo, desde a definição dos moldes e os tipos disponíveis até os materiais utilizados e as inovações que estão ditando as tendências do setor. Compreender as vantagens da fabricação de moldes de injeção e aplicar práticas de manutenção adequadas também são aspectos fundamentais para garantir a durabilidade e a eficácia desses moldes. À medida que a indústria avança, as empresas que se adaptam a essas mudanças e adotam novas tecnologias estarão bem posicionadas para atender à demanda crescente por produtos personalizados e sustentáveis. Portanto, investir na atualização e capacitação no campo da fabricação de moldes de injeção é essencial para qualquer negócio que busque se destacar e prosperar em um mercado competitivo.