Fabricação de Moldes para Injeção de Plásticos Eficazes
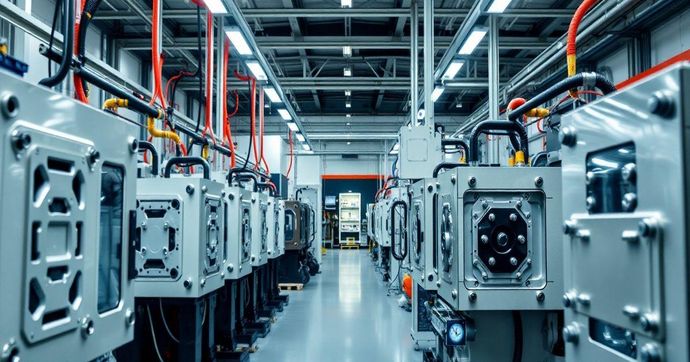
Por: Leonardo - 29 de Dezembro de 2024
A fabricação de moldes para injeção de plásticos desempenha um papel fundamental na produção de diversos produtos que usamos diariamente. Este processo não apenas garante a precisão e a qualidade das peças, mas também otimiza a eficiência na produção em massa. Neste artigo, vamos explorar os principais aspectos da fabricação de moldes, desde os diferentes tipos e materiais utilizados até as tecnologias mais modernas que estão revolucionando a indústria. Continue lendo para descobrir como essa prática é essencial para o sucesso na fabricação de plásticos.
Importância da Fabricação de Moldes para Injeção de Plásticos
A fabricação de moldes para injeção de plásticos é uma etapa crucial na cadeia produtiva de diversas indústrias. Moldes bem projetados e fabricados garantem não apenas a qualidade dos produtos finais, mas também a eficiência e a economia no processo de produção. Neste contexto, a necessidade de moldes de alta qualidade se torna evidente, uma vez que eles são responsáveis pela definição das características e especificações das peças que serão produzidas.
Um dos principais benefícios da fabricação de moldes para injeção de plásticos é a sua capacidade de replicar com precisão designs complexos. Isso é especialmente importante em setores como automotivo, eletrônico e de bens de consumo, onde a estética e a funcionalidade das peças são fundamentais. Com moldes bem projetados, é possível produzir milhares de unidades com exatidão milimétrica, reduzindo o desperdício de material e minimizando os custos.
Outro ponto a ser destacado é a agilidade que a fabricação de moldes proporciona. A produção em massa de peças plásticas requer linhas de montagem que sejam rápidas e eficientes. Com moldes de qualidade, o tempo de ciclo do processo de injeção é significativamente reduzido, permitindo uma maior produtividade. Isso é essencial para atender à demanda do mercado, especialmente em tempos de alta competitividade.
Além disso, a fabricação de moldes para injeção de plásticos contribui para a sustentabilidade dos processos industriais. Moldes bem projetados, que utilizam tecnologias avançadas, ajudam a diminuir o consumo de energia e a geração de resíduos. Isto é fundamental em um cenário onde as empresas estão cada vez mais preocupadas com a sustentabilidade e a redução de seu impacto ambiental. A indústria tem adotado práticas que visam não apenas a eficiência econômica, mas também a responsabilidade social e ambiental.
As empresas de injeção plástica precisam entender a importância de investir em moldes de alta qualidade desde o início do projeto. Moldes mal projetados ou mal fabricados podem resultar em falhas nas peças, levando a retrabalhos e desperdício de material, o que gera custos extras e diminui a competitividade nos mercados. Portanto, o investimento em moldes eficazes é um dos primeiros passos para garantir o sucesso de uma linha de produção.
Outro aspecto relevante é a versatilidade que os moldes de injeção de plásticos oferecem. Esses moldes podem ser projetados para atender uma ampla gama de produtos, desde pequenos componentes eletrônicos até grandes peças para automóveis. Essa adaptabilidade é essencial em um mercado que valoriza a personalização e a inovação. Os moldes podem ser alterados e ajustados para atender a modificações no design, permitindo que as empresas se adaptem rapidamente às novas demandas do mercado e tendências de consumo.
Por fim, a atuação de profissionais experientes na fabricação de moldes é fundamental. Engenheiros e designers que conhecem as nuances do processo de injeção de plásticos podem criar moldes que não apenas atendem às especificações técnicas, mas que também são otimizados para a produção em larga escala. O know-how acumulado ao longo dos anos no desenvolvimento de moldes é um diferencial competitivo que pode definir o sucesso ou fracasso de um projeto.
Em resumo, a importância da fabricação de moldes para injeção de plásticos não pode ser subestimada. Moldes de qualidade garantem precisão, eficiência, sustentabilidade e versatilidade, fatores que são imprescindíveis para a competitividade das empresas no cenário atual. Assim, investir em moldes adequados deve ser encarado como uma prioridade para qualquer negócio que deseje se destacar no mercado e atender às exigências dos clientes com excelência.
Processo de Fabricação de Moldes
O processo de fabricação de moldes é uma etapa fundamental na indústria de injeção de plásticos, pois define a qualidade e a precisão das peças produzidas. Este processo envolve várias etapas, desde a concepção inicial até a finalização do molde, e exige a união de tecnologia avançada, habilidades técnicas e conhecimento profundo dos materiais utilizados.
O primeiro passo no processo de fabricação de moldes é o desenvolvimento do projeto. Nesta fase, engenheiros e designers trabalham em conjunto para criar um modelo tridimensional (3D) do molde desejado. Utilizando softwares de CAD (Desenho Assistido por Computador), é possível simular a produção e identificar falhas potenciais antes mesmo da fabricação. Essa etapa é crucial, pois um bom projeto é a base para um molde funcional e eficiente.
Após a finalização do projeto, o próximo passo é a seleção dos materiais. A escolha do material para a confecção do molde é uma decisão importante, já que influenciará diretamente na durabilidade e na performance do molde. Os materiais mais comuns utilizados na fabricação de moldes incluem aço e alumínio. O aço é conhecido por sua resistência e durabilidade, sendo a escolha preferida para produções em larga escala. Por outro lado, o alumínio é mais leve e pode ser mais econômico, sendo frequentemente utilizado para protótipos e produções menores.
Uma vez definidos o projeto e os materiais, inicia-se a etapa de usinagem. A usinagem é o processo de transformar o material bruto em componentes que comporão o molde. Isso é feito utilizando máquinas-ferramenta de alta precisão, como fresadoras, tornos e cortadoras a laser. Na usinagem, as dimensões do molde são rigorosamente respeitadas, garantindo que cada parte se encaixe perfeitamente no todo. A precisão nesta fase é fundamental, pois pequenas variações podem resultar em falhas na produção das peças injetadas.
Após a usinagem, os componentes do molde são montados. Essa fase envolve a união de diversas partes que foram fabricadas separadamente, como cavidades, canais de resfriamento e sistemas de ejeção. A montagem requer habilidade e conhecimento técnico, pois cada componente deve ser posicionado de maneira a funcionar eficientemente durante o processo de injeção.
Uma etapa igualmente importante é a polimento e acabamento do molde. Isso garante que as superfícies internas do molde estejam lisas, evitando imperfeições nas peças produzidas. Essa fase é vital para garantir que as peças sejam retiradas facilmente do molde após o processo de injeção. Além disso, um bom acabamento contribui para a estética da peça final, algo essencial em mercados que valorizam a aparência dos produtos.
Outro aspecto do processo de fabricação de moldes é a realização de testes. Antes de iniciar a produção em grande escala, é fundamental realizar uma série de testes para verificar se o molde está funcionando corretamente. Isso envolve a injeção de plásticos de teste e a análise das peças resultantes. Os testes podem identificar problemas como vazamentos, falhas de ejeção ou defeitos de superfície que precisam ser corrigidos antes da produção em massa.
É aqui que a ferramentaria de moldes plasticos desempenha um papel vital, fornecendo o suporte necessário para ajustes e refinamentos. Constatados os problemas, as correções podem ser feitas no molde para assegurar que ele atenda a todas as especificações técnicas.
Depois que todos os testes são realizados e as correções feitas, o molde está pronto para ser enviado à linha de produção. Um molde bem desenvolvido e fabricado pode ter uma longa vida útil, suportando milhares de ciclos de produção antes de necessitar de manutenção ou substituição. Isso torna o investimento em moldes de alta qualidade essencial para a rentabilidade de qualquer operação de injeção de plásticos.
Em resumo, o processo de fabricação de moldes é complexo e envolve várias etapas interligadas, cada uma delas crucial para a qualidade do produto final. Desde o projeto inicial até a produção em larga escala, a atenção aos detalhes, a escolha dos materiais, a usinagem precisa e a realização de testes são fundamentais para garantir o sucesso do processo de fabricação. Assim, investir tempo e recursos nessa etapa é fundamental para garantir a excelência nas peças produzidas e a competitividade no mercado.
Materiais Utilizados na Fabricação de Moldes
A seleção dos materiais é um dos aspectos mais críticos na fabricação de moldes para injeção de plásticos. A escolha correta dos materiais não apenas afeta a durabilidade e a eficiência do molde, mas também a qualidade das peças que serão produzidas. Existem vários tipos de materiais utilizados na fabricação de moldes, cada um com suas características específicas e aplicações adequadas. Este conteúdo irá explorar os principais materiais empregados nesse processo.
Um dos materiais mais tradicionais e amplamente utilizados na fabricação de moldes é o aço. O aço é conhecido por sua resistência e durabilidade, o que o torna ideal para aplicações em que o molde passará por um alto número de ciclos de produção. No entanto, o tipo de aço escolhido pode variar bastante. Aços carbono, aços de liga e aços ferramenta são os mais comuns.
Dentre os aços ferramenta, destacam-se o Aço D2 e o Aço P20, que são populares por suas propriedades de dureza e resistência ao desgaste. O Aço D2, por exemplo, é um aço de alta resistência ao desgaste, que se mantém duro mesmo em temperaturas elevadas, tornando-o muito eficaz para aplicações que exigem alta precisão e durabilidade. Por outro lado, o Aço P20 é frequentemente usado para moldes de injeção de plásticos devido à sua usinabilidade superior e à boa resistência ao desgaste.
Outro material que vem ganhando destaque na fabricação de moldes é o alumínio. O alumínio é um material mais leve que o aço e apresenta uma excelente condutividade térmica, o que pode ser vantajoso em processos que exigem um rápido resfriamento. A escolha do alumínio é frequentemente feita para moldes que serão utilizados em produções menores ou de protótipos, devido aos menores custos e à rapidez na fabricação. O alumínio também pode ser tratado para aumentar sua dureza, o que o torna uma opção prática e versátil.
Além do aço e do alumínio, os materiais compósitos também estão se tornando cada vez mais populares na indústria de moldes. Os compósitos são misturas de materiais que podem combinar os melhores atributos de cada componente. Por exemplo, compósitos de fibra de carbono podem ser utilizados em situações onde a leveza e a resistência são necessárias. Estes materiais são especialmente úteis em aplicações industriais modernas, onde a inovação é uma prioridade.
Outro aspecto a ser considerado na seleção de materiais é a resistência química. Em muitos casos, os moldes precisarão lidar com plásticos que contêm aditivos ou corantes que podem atacar o material do molde. Portanto, é importante selecionar materiais que sejam resistents a essas substâncias. Aqui, o aço inoxidável se destaca, pois possui maior resistência à corrosão e, portanto, pode ser uma escolha vantajosa para algumas aplicações específicas.
A escolha do material também deve ser feita levando em consideração o custo e a vida útil do molde. Materiais de alta qualidade muitas vezes exigem um investimento inicial mais elevado, mas podem ter uma vida útil significativamente mais longa, o que gera economia em termos de manutenção e substituição ao longo do tempo. Portanto, é preciso avaliar corretamente a relação custo-benefício durante o planejamento da fabricação dos moldes.
No contexto da ferramentaria e usinagem, a escolha do material adequado também impacta as práticas de usinagem que serão utilizadas. Materiais mais duros podem exigir técnicas e ferramentas de usinagem especializadas, aumentando o tempo e o custo do processo. Por outro lado, materiais que são mais fáceis de usinar podem acelerar a fabricação do molde, mas podem sacrificar a durabilidade a longo prazo.
Finalmente, um fator que não pode ser ignorado é a inovação tecnológica no campo dos materiais. Nos últimos anos, novas ligas e materiais avançados têm surgido, proporcionando melhores soluções para a fabricação de moldes. Pesquisas em polímeros avançados, por exemplo, têm mostrado resultados promissores em aplicações industriais. Portanto, manter-se atualizado com as novas tendências e inovações pode proporcionar vantagens competitivas significativas.
Em resumo, a escolha dos materiais utilizados na fabricação de moldes é um processo que deve levar em consideração diversos fatores, incluindo a durabilidade, a resistência química, o custo e a usinabilidade. O uso de materiais adequados não só maximiza a eficiência do molde, mas também garante a qualidade das peças produzidas. Assim, a seleção criteriosa de materiais é essencial para o sucesso de qualquer projeto de fabricação na indústria de injeção de plásticos.
Tipos de Moldes para Injeção de Plásticos
A injeção de plásticos é um dos processos de fabricação mais utilizados na indústria moderna, permitindo a produção de uma ampla variedade de peças e componentes de diferentes tamanhos e complexidades. Para garantir a eficiência e a qualidade no processo de injeção, é fundamental escolher o tipo adequado de molde. Neste artigo, vamos explorar os principais tipos de moldes utilizados na injeção de plásticos e suas aplicações específicas.
Um dos tipos mais comuns de moldes para injeção de plásticos é o molde de cavidade simples. Este tipo de molde é projetado para produzir uma única peça por ciclo de injeção. Os moldes de cavidade simples são frequentemente usados para produtos que não exigem produção em massa, como protótipos e peças únicas. Embora sejam menos complexos e mais fáceis de fabricar, eles podem ser menos eficientes em termos de custo e tempo, especialmente quando a demanda é alta.
Em contrapartida, os moldes de cavidade múltipla são projetados para produzir várias peças simultaneamente em um único ciclo de injeção. Esse tipo de molde é ideal para produções em larga escala, pois permite uma maior eficiência e redução de custos. Moldes de cavidade múltipla são frequentemente utilizados em produtos de consumo, como tampas, garrafas e outros itens descartáveis. No entanto, a complexidade em seu design e fabricação pode aumentar os custos iniciais.
Outro tipo bastante utilizado é o molde de injeção por sopro, que é especificamente projetado para a produção de peças ocas, como garrafas e recipientes plásticos. Esse processo envolve a introdução de um tubo de plástico derretido em um molde, onde o ar é soprado para expandir o material e preencher as cavidades do molde. Este método é especialmente útil para aplicações que exigem paredes finas e leves. Com o crescente uso de embalagens plásticas, os moldes de sopro se tornaram indispensáveis na indústria.
Os moldes de injeção com sistema de resfriamento canalizado também merecem destaque. Esses moldes são projetados com canais internos que permitem a circulação de refrigerante para controlar a temperatura durante o processo de injeção. O resfriamento eficiente é vital para garantir a qualidade das peças moldadas, pois minimiza distorções e reduz o tempo de ciclo. Com a evolução das técnicas de fabricação, esses sistemas de resfriamento também se tornaram mais sofisticados, permitindo um controle ainda mais preciso da temperatura.
Além desses, os moldes de injeção de dois componentes (multi-material) estão se tornando cada vez mais populares. Esses moldes permitem a injeção de dois tipos diferentes de plásticos em uma única peça, criando produtos com propriedades variadas, como resistência a impacto e flexibilidade. Moldes de dois componentes são frequentemente utilizados em produtos que necessitam de uma combinação de características, como utensílios de cozinha e componentes automotivos. Essa tecnologia é um exemplo de como a inovação na injeção de plastico está ampliando as possibilidades de design e funcionalidade dos produtos.
Os moldes de injeção descartáveis são outra categoria a ser mencionada. Eles são projetados para produção em um volume muito alto, mas com um ciclo de vida muito curto. Esses moldes são frequentemente utilizados em indústrias onde os produtos são consumíveis, como embalagens alimentícias. A principal vantagem dos moldes descartáveis é o baixo custo inicial e a capacidade de produzir grandes quantidades rapidamente.
Por fim, os moldes de injeção de alta precisão também são uma categoria importante. Esses moldes são projetados para garantir a máxima exatidão no dimensionamento e nas tolerâncias das peças produzidas. Eles são essenciais em indústrias que requerem componentes altamente tolerantes, como a eletrônica e a aeronáutica. Esse tipo de molde normalmente envolve processos de fabricação mais avançados e um controle de qualidade rigoroso.
É fundamental que as empresas que atuam na injeção de plásticos compreendam as diferenças entre esses tipos de moldes e suas respectivas aplicações. A escolha errada do molde pode não apenas comprometer a qualidade do produto final, mas também impactar nos custos de produção e no tempo de entrega. Portanto, uma análise cuidadosa das necessidades de produção, juntamente com o conhecimento técnico sobre os tipos de moldes disponíveis, garantirá que a empresa possa atender às expectativas dos clientes de forma eficaz.
Em resumo, os diferentes tipos de moldes para injeção de plásticos desempenham um papel crucial na eficiência e na qualidade do processo de fabricação. Cada tipo de molde tem suas características, vantagens e desvantagens, tornando essencial a escolha cuidadosa de acordo com as demandas do produto a ser fabricado. Com o avanço contínuo da tecnologia e a inovação nos processos de produção, as possibilidades para a criação de moldes e peças plásticas continuam a expandir, oferecendo novos desafios e oportunidades.
Tecnologias Inovadoras na Fabricação de Moldes
A fabricação de moldes para injeção de plásticos está em constante evolução, impulsionada pelo avanço tecnológico e pela demanda por eficiência e qualidade na produção. Tecnologias inovadoras estão transformando a maneira como os moldes são projetados e fabricados, proporcionando melhorias significativas em desempenho, durabilidade e flexibilidade. Neste artigo, vamos explorar algumas das principais tecnologias que estão moldando o futuro da fabricação de moldes.
Uma das inovações mais significativas na fabricação de moldes é a utilização de impressão 3D. Essa tecnologia permite a criação de protótipos rápidos e a fabricação de componentes complexos que, de outra forma, seriam difíceis ou até impossíveis de produzir com métodos tradicionais. A impressão 3D permite a experimentação e iteração no design de moldes, reduzindo consideravelmente o tempo de desenvolvimento. Além disso, a impressão de moldes em 3D reduz o desperdício de material, já que utiliza apenas a quantidade necessária para a construção do molde.
A impressão 3D também permite a criação de estruturas internas complexas, como canais de resfriamento que podem ser otimizados para melhorar a eficiência térmica durante a injeção. Esses canais permitem um resfriamento uniforme, minimizando deformações e aumentando a qualidade das peças produzidas. A personalização e a produção sob demanda são outras vantagens que a impressão 3D oferece, permitindo que empresas se adaptem rapidamente às necessidades do mercado.
Outra tecnologia inovadora é a usinagem de precisão por meio de máquinas CNC (Controle Numérico Computadorizado). As máquinas CNC permitem a fabricação de moldes com tolerâncias extremas, garantindo que as peças produzidas sejam exatas em suas dimensões. Com o uso de software avançado, os operadores podem criar programas que controlam o movimento das ferramentas de usinagem, resultando em um processo altamente eficiente e repetível. O uso de máquinas CNC também reduz a necessidade de intervenção manual, aumentando a segurança e a consistência na produção.
A soldagem a laser é outra forma inovadora de unir componentes de moldes de forma eficiente e precisa. Essa técnica permite a fusão de materiais com extrema precisão, resultando em juntas fortes e duráveis. A soldagem a laser é especialmente útil na fabricação de moldes com geometrias complexas, onde a união de diferentes partes deve ser realizada sem causar deformações. Além disso, essa técnica minimiza a necessidade de tratamento adicional nas superfícies, economizando tempo e recursos.
As tecnologias de revestimento também estão desempenhando um papel importante na fabricação de moldes. Revestimentos avançados, como nitretação e coatings de carbono, podem ser aplicados às superfícies dos moldes para melhorar sua resistência ao desgaste e à corrosão. Esses revestimentos aumentam significativamente a vida útil dos moldes, resultando em menor necessidade de manutenção e substituições. Com a aplicação correta de revestimentos, os moldes podem operar em condições severas sem comprometer a qualidade das peças produzidas.
A automação industrial é outra tendência crescente na fabricação de moldes. Sistemas automatizados podem ser utilizados para o manuseio de materiais, supervisão de processos e controle de qualidade. Isso não apenas aumenta a eficiência operacional, mas também reduz o potencial de erros humanos. A automação integrada com tecnologias de inteligência artificial também pode prever falhas e otimizar processos em tempo real, aumentando a confiabilidade e a produtividade da linha de produção.
Além disso, a modelagem e simulação avançadas por computador têm se tornado essenciais no desenvolvimento de moldes. Softwares de simulação permitem que designers e engenheiros analisem o comportamento do molde e do material durante o processo de injeção, identificando possíveis problemas antes da fabricação real. Essa abordagem proativa ajuda a evitar falhas e melhora a qualidade do produto final, economizando tempo e recursos.
As tecnologias de comunicação e monitoramento também estão se integrando à fabricação de moldes. Com a Internet das Coisas (IoT), máquinas e equipamentos podem ser conectados em rede, permitindo o monitoramento em tempo real e a análise de dados. Isso proporciona uma visão abrangente do desempenho do molde e do processo de injeção, possibilitando a identificação de melhorias e a tomada de decisões informadas.
Por fim, a pesquisa contínua e o desenvolvimento de novos materiais têm sido um motor fundamental para inovações na fabricação de moldes. Materiais compósitos, polímeros de alto desempenho e ligas metálicas avançadas estão ampliando as possibilidades de design e funcionalidade de moldes. Com esses novos materiais, os engenheiros podem criar moldes mais leves, duráveis e eficientes, atendendo a uma variedade ainda maior de aplicações industriais.
Em resumo, as tecnologias inovadoras na fabricação de moldes estão mudando a forma como os produtos são fabricados. Através da impressão 3D, usinagem CNC, soldagem a laser, revestimentos avançados, automação industrial e simulação por computador, as empresas estão se equipando para enfrentar os desafios do mercado moderno. O investimento em tecnologias emergentes não apenas melhora a eficiência, mas também assegura a qualidade e a competitividade no setor de injeção de plásticos, criando um futuro promissor para a indústria.
Cuidados na Manutenção de Moldes
A manutenção adequada de moldes para injeção de plásticos é essencial para garantir a longevidade e a eficiência dos equipamentos. Moldes bem conservados não apenas prolongam a vida útil do ativo, como também garantem que as peças produzidas mantenham a qualidade e a precisão esperadas. Neste artigo, abordaremos os principais cuidados que devem ser tomados na manutenção de moldes, além de discutir a importância de práticas de manutenção adequadas.
Um dos primeiros aspectos a serem considerados na manutenção de moldes é a limpeza regular. Após cada ciclo de produção, é fundamental limpar o molde para remover quaisquer resíduos de plástico ou outros materiais que possam ter se acumulado. A sujeira e os depósitos podem afetar o funcionamento adequado do molde, causando falhas na produção e prejudicando a qualidade das peças. Recomenda-se utilizar ferramentas apropriadas e produtos de limpeza que não danifiquem as superfícies do molde. A limpeza regular ajuda a prevenir a corrosão e a deterioração dos materiais.
Além da limpeza, a lubrificação adequada é essencial para o bom funcionamento dos moldes. O uso de lubrificantes apropriados nas partes móveis do molde, como os sistemas de ejeção, pode reduzir o atrito e o desgaste, prolongando a vida dos componentes. A lubrificação deve ser realizada com produtos recomendados pelos fabricantes e em intervalos regulares, conforme a utilização do molde. Um molde bem lubrificado opera de maneira mais suave, o que resulta em menos falhas e interrupções durante a produção.
Outro cuidado importante é a verificação e o ajuste das partes do molde. Com o tempo, e com o intenso uso, algumas partes podem se desgastar ou se desajustar. A realização de inspeções periódicas permite identificar desgastes, folgas ou danos que possam comprometer a qualidade das peças moldadas. Qualquer ajuste necessário deve ser feito imediatamente para evitar problemas maiores no futuro. A calibragem e o alinhamento dos componentes também são essenciais para assegurar que o molde funcione conforme as especificações projetadas.
A proteção contra corrosão é uma preocupação constante na manutenção de moldes, especialmente para aqueles que são fabricados em aço. Moldes expostos a um ambiente úmido ou que entram em contato com materiais corrosivos podem sofrer danos significativos. É importante aplicar um revestimento protetor nas superfícies dos moldes, como óleos ou sprays anticorrosivos, e armazená-los em condições adequadas quando não estiverem em uso. A proteção preventiva é uma maneira eficaz de garantir a integridade do molde e evitar custos futuros com reparos.
Uma prática fundamental que deve ser implementada na manutenção de moldes é o registro e documentação de todas as operações de manutenção realizadas. Manter um histórico detalhado das limpezas, lubrificações, inspeções e quaisquer reparos feitos ajuda a identificar padrões de desgaste e a prever problemas antes que se tornem críticos. A gestão de informações também facilita a tomada de decisões sobre a necessidade de substituições ou atualizações. Essa prática é especialmente valiosa para empresas que possuem um grande número de moldes e desejam otimizar suas operações.
Outro ponto a ser considerado é a formação e capacitação da equipe envolvida na manutenção de moldes. Funcionários bem treinados e capacitados são essenciais para garantir a execução das práticas de manutenção corretamente. Isso inclui não apenas o conhecimento técnico sobre o funcionamento dos moldes, mas também sobre os cuidados necessários para prolongar sua vida útil. Investir no treinamento da equipe é um passo fundamental para assegurar a eficiência da manutenção e a qualidade dos produtos moldados.
Além disso, promover um ambiente de trabalho seguro e organizado dentro do local onde os moldes são mantidos é crucial. A desorganização pode levar a acidentes e danos aos moldes, além de comprometer a eficiência dos processos de manutenção. Com um espaço de trabalho limpo e arrumado, a equipe pode realizar as operações de manutenção com mais eficiência e segurança. O planejamento adequado das rotinas de manutenção também é vital para minimizar as interrupções nas linhas de produção.
Por fim, é imprescindível a realização de manutenções programadas. Isso envolve a definição de um cronograma claro para as atividades de manutenção e inspeção, de forma que cada molde passe pela manutenção em intervalos regulares. Isso não apenas ajuda a evitar falhas imprevistas, mas também garante que a produção seja mantida em um nível de qualidade consistente ao longo do tempo.
Em resumo, a manutenção de moldes para injeção de plásticos é uma tarefa que exige atenção e disciplina. Com práticas de limpeza, lubrificação, inspeção, proteção contra corrosão e documentação devidamente implementadas, as empresas podem prolongar significativamente a vida útil de seus moldes e garantir a qualidade das peças produzidas. Implementar um programa de manutenção eficaz é uma estratégia que não apenas melhora a eficiência operacional, mas também resulta em economia a longo prazo e maior satisfação do cliente.
Vantagens da Fabricação de Moldes Sob Medida
A fabricação de moldes sob medida é uma abordagem que vem ganhando cada vez mais espaço na indústria de injeção de plásticos. Diferente dos moldes padrão, os moldes personalizados são projetados especificamente para atender às necessidades e requisitos de um cliente ou projeto específico. Essa adaptabilidade traz uma série de vantagens que podem impactar não apenas a qualidade do produto final, mas também a eficiência operacional e o retorno sobre o investimento. Vamos explorar as principais vantagens da fabricação de moldes sob medida.
Uma das maiores vantagens da fabricação de moldes sob medida é a capacidade de atender a especificações exatas e únicas de design. Cada projeto pode ter requisitos específicos em termos de formato, dimensões e funcionalidades que moldes padrão muitas vezes não conseguem atender. Com moldes personalizados, é possível criar peças que se ajustem perfeitamente ao objetivo desejado, resultando em produtos finais de qualidade superior. Essa precisão no design é particularmente importante em indústrias que exigem altos padrões de tolerância, como a automotiva e a eletrônica.
Além disso, a fabricação de moldes sob medida proporciona uma maior flexibilidade para a produção. Os moldes personalizados podem ser projetados para facilitar alterações no formato ou nas características das peças, permitindo que os fabricantes se adaptem rapidamente às mudanças nas demandas do mercado ou nas preferências dos clientes. Isso é crucial em um ambiente de negócios dinâmico, onde os consumidores estão cada vez mais exigentes por inovações e personalizações de produtos. Moldes sob medida possibilitam uma abordagem proativa em relação às tendências de mercado.
Outro benefício significativo é a otimização dos processos de produção. Moldes personalizados são projetados levando em consideração o material que será injetado e as condições de operação específicas da máquina. Isso garante que o processo de injeção ocorra de forma mais eficiente, reduzindo falhas e minimizando desperdícios de material. A personalização do molde pode incluir características como canais de resfriamento otimizados e sistemas de ejeção que melhoram o fluxo do material, aumentando assim a produtividade e a consistência na produção.
A economia a longo prazo também é uma vantagem significativa da fabricação de moldes sob medida. Embora o custo inicial da fabricação de moldes personalizados possa ser maior do que o de moldes padrão, a eficiência melhorada e a redução de custos operacionais, como menos retrabalhos e desperdícios, podem compensar esse investimento. Com a produção de peças de alta qualidade que atendem exatamente às necessidades do cliente, a satisfação do cliente é aumentada, resultando em vendas e receita mais altas.
Ademais, a fabricação de moldes sob medida permite um controle maior sobre o processo de produção e os padrões de qualidade. Os fabricantes podem implementar rigorosos controles de qualidade durante a produção dos moldes, desde a escolha dos materiais até os processos de usinagem e teste. Isso se traduz em moldes que são mais confiáveis e duráveis, o que é essencial para a produção de peças que serão utilizadas em aplicações críticas. Moldes bem fabricados minimizam a necessidade de manutenção e reparos frequentes.
Outra vantagem importante é a possibilidade de inovação. A fabricação de moldes sob medida permite que os designers e engenheiros experimentem novas idéias e abordagens que podem não ser viáveis com moldes padrão. A personalização pode descobrir novas soluções de design, que podem resultar em produtos finais mais eficientes e tecnologicamente avançados. Isso destaca a importância da inovação como um diferencial competitivo em setores saturados.
Além disso, moldes personalizados criam a oportunidade para o desenvolvimento de produtos exclusivos ou de nicho, que atendem a mercados específicos. Alguns fabricantes se especializam em produzir itens únicos ou de baixa tiragem, e a fabricação de moldes sob medida é especialmente benéfica nesse contexto. Produtos personalizados podem se destacar no mercado, atraindo uma base de clientes que busca exclusividade e diferenciação.
A personalização dos moldes também pode aumentar a sustentabilidade do processo de fabricação. Moldes sob medida são frequentemente projetados para utilizar menos material ou para otimizar a utilização do material, ajudando assim a diminuir o desperdício. Além disso, moldes que são fabricados com foco na eficiência energética contribuem para a redução da pegada de carbono da produção, o que é um aspecto cada vez mais valorizado pelos consumidores e pela sociedade em geral.
Em resumo, a fabricação de moldes sob medida traz uma ampla gama de benefícios que são essenciais em um ambiente industrial moderno e competitivo. Desde a precisão no design e flexibilidade na produção até a otimização de processos e segurança em relação à qualidade, as vantagens dos moldes personalizados podem ter um impacto sustentado nas operações de uma empresa. À medida que as indústrias continuam a evoluir, investir na fabricação de moldes sob medida se torna uma estratégia valiosa para quem busca se destacar no mercado conforme as demandas e expectativas dos consumidores se transformam.
Erros Comuns na Fabricação de Moldes e Como Evitá-los
A fabricação de moldes para injeção de plásticos é um processo complexo que exige precisão, atenção aos detalhes e uma compreensão aprofundada das técnicas e materiais utilizados. No entanto, mesmo com todas essas considerações, alguns erros comuns podem ocorrer e resultar em prejuízos significativos tanto financeiros quanto em termos de qualidade do produto final. Neste artigo, exploraremos os erros mais frequentes na fabricação de moldes e forneceremos orientações sobre como evitá-los.
Um dos erros mais comuns na fabricação de moldes é a inadequação entre o design do molde e o processo de injeção. Isso pode ocorrer quando o projetista não leva em consideração as características do material que será utilizado, a temperatura de injeção adequada ou as especificações da máquina de injeção. A falta de alinhamento entre esses fatores pode levar a problemas como deformações, trincas ou falhas na ejeção das peças. Para evitar esse erro, é fundamental que o design do molde seja desenvolvido em estreita colaboração com os especialistas em injeção e considerando todas as variáveis operacionais.
Outro erro frequente é a escolha inadequada dos materiais do molde. O material utilizado para a fabricação do molde deve ser escolhido com base na aplicação específica e nas condições em que o molde será utilizado. A utilização de um material que não tenha a resistência necessária ao desgaste ou à temperatura pode resultar em um molde com vida útil curta, que exige reparos frequentes. Para evitar esse problema, é essencial realizar uma análise detalhada sobre as propriedades do material, alinhando sua escolha com as exigências do projeto e o ciclo de vida esperado do molde.
Além disso, a falta de comunicação entre a equipe de design, a equipe de engenharia e a linha de produção pode gerar desentendimentos e consequentemente, erros. Um molde mal projetado pode resultar em uma peça que não atende às especificações esperadas. Isso pode ser minimizado através de reuniões regulares e revisões em conjunto das especificações do molde antes e durante seu processo de fabricação. A transparência na comunicação facilita a identificação precoce de problemas e a realização das correções necessárias.
A manutenção inadequada dos moldes é outro ponto crucial que não deve ser negligenciado. Moldes que não recebem a devida manutenção podem apresentar desempenho abaixo do esperado, resultando em produtos com qualidade inferior. Além disso, a falta de cuidados pode levar a danos irreversíveis que, em última análise, requerem substituição do molde. Para evitar esse erro, é importante estabelecer um cronograma de manutenção regular, que inclua limpeza, lubrificação e inspeção dos componentes do molde. Isso não só melhora o desempenho do molde, mas também aumenta sua durabilidade.
Quanto à usinagem, erros na execução dessa fase podem levar a imprecisões geométricas que afetam o ajuste e o funcionamento do molde. A utilização de máquinas e ferramentas inadequadas para a usinagem pode resultar em acabamentos que não atendem às especificações de tolerância. Para minimizar esses problemas, é crucial escolher equipamentos de usinagem apropriados e realizar calibrações regulares, além de monitorar o desempenho da usinagem com rigor para garantir a máxima precisão.
Outro erro comum acontece durante o teste do molde. Negligenciar esta fase ou não realizar uma série de testes abrangentes pode levar à produção de peças com falhas. Testar o molde sob condições reais de operação é vital para identificar possíveis problemas antes de iniciar a produção em massa. Para evitar essa armadilha, os testes devem ser uma parte inegociável do processo de fabricação, com atenção especial dedicada a fichas de desempenho que possibilitem encontrar pontos de melhoria.
Além disso, a falta de um plano de contingência para resolver problemas que possam surgir durante a fabricação pode resultar em atrasos significativos. Ter um plano bem estruturado para lidar com falhas e imprevistos é fundamental para minimizar os impactos negativos nas operações. Isso inclui a capacitação da equipe para agir rapidamente em situações de crise e a gestão de fornecedores para garantir que os materiais críticos estejam sempre disponíveis.
Por fim, erros na documentação e registro das operações realizadas podem causar problemas futuros. Não manter um histórico atualizado sobre cada etapa do processo de fabricação pode dificultar a identificação de falhas ou a realização de melhorias. Para evitar esse erro, recomenda-se a implementação de um sistema de gestão documental que integre informações sobre o design, materiais utilizados, manutenções e testes realizados, assegurando que todos os envolvidos no processo tenham acesso aos dados relevantes.
Em suma, a fabricação de moldes para injeção de plásticos é um processo que demanda cuidado e precisão em cada etapa. Ao evitar erros comuns como inadequação no design, escolha errada de materiais, falta de comunicação, manutenção inadequada, usinagem imprecisa, testes insuficientes e falhas na documentação, as empresas conseguem garantir a produção de peças de alta qualidade, minimizar desperdícios e otimizar a eficiência operacional. Investir na prevenção de erros é uma estratégia essencial para alcançar consistência e sucesso na fabricação de moldes.
Em conclusão, a fabricação de moldes para injeção de plásticos se revela um elemento-chave na cadeia produtiva, impactando diretamente a qualidade e a eficiência dos produtos finais que encontramos em nosso dia a dia. Ao abordar desde os tipos e materiais utilizados até as mais recentes inovações tecnológicas e os cuidados necessários na manutenção, é evidente que esse processo não pode ser subestimado. A atenção aos detalhes, à precisão no design, à escolha adequada dos materiais e à implementação de tecnologias avançadas garantem que os moldes atendam às especificações exigidas pelos diversos setores. Além disso, evitar erros comuns na fabricação é primordial para otimizar a produtividade e assegurar a qualidade das peças. Portanto, para empresas que desejam se destacar em um mercado cada vez mais competitivo, investir na fabricação de moldes de qualidade e na adoção de boas práticas é essencial para garantir não apenas a satisfação do cliente, mas também a sustentabilidade e o sucesso a longo prazo.