Moldes Injeção Plástica: Como Escolher e Otimizar sua Produção
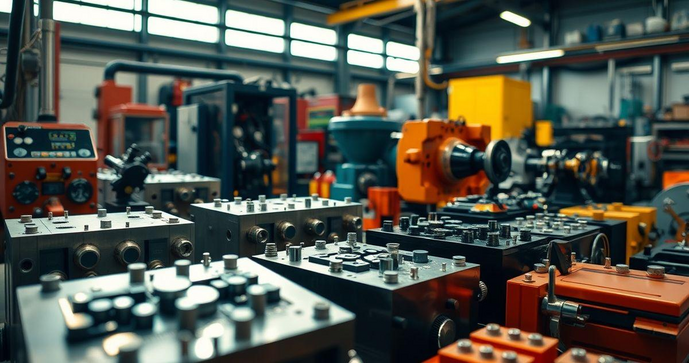
Por: Leonardo - 26 de Janeiro de 2025
Moldes injeção plástica desempenham um papel crucial na fabricação de produtos plásticos, permitindo a produção em larga escala com precisão e eficiência. Neste artigo, abordaremos os diferentes tipos de moldes, fatores a serem considerados na escolha, o processo de fabricação e as vantagens da injeção plástica. Além disso, discutiremos a manutenção necessária e as tendências atuais que estão moldando o futuro dessa tecnologia. Acompanhe e descubra como otimizar sua produção com moldes de injeção plástica.
1. Tipos de Moldes para Injeção Plástica
Os moldes para injeção plástica são fundamentais para a produção de uma ampla variedade de produtos, desde componentes eletrônicos até utensílios domésticos. A escolha do tipo de molde adequado pode impactar diretamente a qualidade do produto final, a eficiência do processo de produção e os custos envolvidos. Existem diversos tipos de moldes, cada um projetado para atender a necessidades específicas. A seguir, exploraremos os principais tipos de moldes utilizados na injeção plástica.
Um dos tipos mais comuns de moldes é o molde de cavidade única. Este tipo de molde é projetado para produzir uma única peça por ciclo de injeção. É ideal para produções em menor escala ou para produtos que exigem alta precisão e qualidade. Os moldes de cavidade única são mais simples em termos de design e, geralmente, mais fáceis de fabricar. No entanto, sua eficiência pode ser limitada em comparação com outros tipos de moldes, especialmente quando se busca aumentar a produção.
Em contrapartida, os moldes de múltiplas cavidades são projetados para produzir várias peças em um único ciclo de injeção. Esses moldes são mais complexos e custam mais para serem fabricados, mas oferecem uma eficiência significativamente maior, tornando-os ideais para produções em larga escala. A utilização de moldes de múltiplas cavidades pode reduzir o tempo de ciclo e os custos de produção, tornando-os uma escolha popular entre as empresas de injeção plástica que buscam maximizar a eficiência.
Outro tipo importante é o molde de injeção por sopro, que é utilizado para produzir peças ocas, como garrafas e recipientes. Este processo envolve a injeção de ar em um tubo de plástico derretido, criando uma forma oca. Os moldes de sopro são projetados para suportar pressões elevadas e são frequentemente utilizados na indústria de embalagens. A versatilidade e a capacidade de produzir formas complexas tornam os moldes de sopro uma escolha popular para muitos fabricantes.
Os moldes de injeção de dois componentes são outra opção interessante. Esses moldes permitem a injeção de dois materiais diferentes em um único ciclo, possibilitando a criação de peças com propriedades distintas, como combinações de rigidez e flexibilidade. Essa técnica é especialmente útil na produção de produtos que exigem características específicas, como dispositivos eletrônicos que precisam de isolamento e proteção. A complexidade do design e a necessidade de equipamentos especializados tornam esses moldes mais caros, mas os benefícios em termos de funcionalidade podem justificar o investimento.
Além disso, existem os moldes de injeção de precisão, que são projetados para atender a requisitos rigorosos de tolerância e acabamento superficial. Esses moldes são frequentemente utilizados na fabricação de componentes para indústrias como a automotiva e a eletrônica, onde a precisão é crucial. A fabricação de moldes de precisão requer tecnologia avançada e um alto nível de especialização, mas os resultados podem ser extremamente benéficos em termos de qualidade e desempenho do produto final.
Os moldes de injeção térmica também merecem destaque. Esses moldes utilizam um sistema de aquecimento para manter a temperatura do material durante o processo de injeção, o que pode melhorar a fluidez do plástico e a qualidade da peça final. Essa técnica é especialmente útil para materiais que têm dificuldades em fluir em temperaturas mais baixas. A utilização de moldes térmicos pode resultar em produtos com melhor acabamento e menos defeitos.
Por fim, os moldes de injeção de alumínio e moldes de injeção de aço são duas opções populares em termos de material. Os moldes de alumínio são mais leves e mais fáceis de fabricar, tornando-os ideais para protótipos e produções em pequena escala. Já os moldes de aço são mais duráveis e resistentes ao desgaste, sendo a escolha preferida para produções em larga escala, onde a durabilidade e a resistência são essenciais.
Em resumo, a escolha do tipo de molde para injeção plástica depende de diversos fatores, incluindo o tipo de produto, a escala de produção e os requisitos de qualidade. Compreender as diferenças entre os tipos de moldes disponíveis pode ajudar os fabricantes a tomar decisões informadas e a otimizar seus processos de produção. A colaboração com empresas de injeção plástica especializadas pode ser um passo importante para garantir que as escolhas feitas atendam às necessidades específicas de cada projeto.
2. Fatores a Considerar na Escolha de Moldes
A escolha do molde adequado para injeção plástica é um passo crucial que pode impactar significativamente a eficiência da produção, a qualidade do produto final e os custos envolvidos. Existem diversos fatores que devem ser considerados ao selecionar um molde, e entender cada um deles pode ajudar os fabricantes a tomar decisões mais informadas. A seguir, discutiremos os principais fatores a serem considerados na escolha de moldes para injeção plástica.
Um dos primeiros aspectos a ser avaliado é o material do molde. Os moldes podem ser fabricados a partir de diferentes materiais, como alumínio e aço. Os moldes de alumínio são mais leves e mais fáceis de fabricar, tornando-os ideais para protótipos e produções em pequena escala. No entanto, eles têm uma vida útil mais curta em comparação com os moldes de aço, que são mais duráveis e resistentes ao desgaste. Para produções em larga escala, os moldes de aço são geralmente a melhor escolha, pois oferecem maior resistência e podem suportar ciclos de injeção mais intensos.
Outro fator importante é o design do molde. O design deve ser cuidadosamente planejado para garantir que o molde atenda às especificações do produto final. Isso inclui considerar a geometria da peça, a localização das entradas de injeção e a necessidade de sistemas de resfriamento. Um design bem elaborado pode minimizar problemas durante a injeção, como bolhas de ar e falhas de preenchimento, resultando em produtos de maior qualidade. Além disso, um bom design pode facilitar a manutenção e a limpeza do molde, prolongando sua vida útil.
A complexidade da peça também deve ser levada em conta. Peças com geometrias complexas podem exigir moldes mais sofisticados, o que pode aumentar os custos de fabricação. É importante avaliar se a complexidade da peça justifica o investimento em um molde mais elaborado. Em alguns casos, pode ser mais vantajoso simplificar o design da peça para facilitar a fabricação do molde e reduzir os custos. A colaboração com uma ferramentaria de moldes plasticos especializada pode ajudar a encontrar o equilíbrio certo entre complexidade e custo.
O custo de fabricação do molde é outro fator crucial. Os custos podem variar significativamente dependendo do material, do design e da complexidade do molde. É essencial realizar uma análise de custo-benefício para determinar se o investimento em um molde específico é viável em relação ao volume de produção esperado. Em alguns casos, pode ser mais econômico optar por um molde mais simples, mesmo que isso signifique uma redução na eficiência da produção.
Além disso, a capacidade de produção deve ser considerada. O molde deve ser capaz de atender à demanda de produção esperada, tanto em termos de quantidade quanto de velocidade. Moldes de múltiplas cavidades podem ser uma boa opção para aumentar a capacidade de produção, mas é importante garantir que o equipamento de injeção utilizado seja compatível com o molde escolhido. A escolha de um molde que não atenda à capacidade de produção necessária pode resultar em atrasos e custos adicionais.
A manutenção do molde também é um aspecto importante a ser considerado. Moldes que exigem manutenção frequente podem aumentar os custos operacionais e reduzir a eficiência da produção. É recomendável escolher moldes que sejam projetados para facilitar a manutenção e a limpeza. Além disso, a disponibilidade de peças de reposição e suporte técnico deve ser avaliada, pois isso pode impactar a capacidade de manter o molde em boas condições ao longo do tempo.
Outro fator a ser considerado é a compatibilidade com o material a ser injetado. Diferentes materiais plásticos têm propriedades distintas que podem afetar o desempenho do molde. É importante garantir que o molde seja adequado para o tipo de plástico que será utilizado, levando em conta fatores como temperatura de injeção, viscosidade e tempo de resfriamento. A escolha de um molde que não seja compatível com o material pode resultar em problemas de qualidade e eficiência.
Por fim, a tecnologia de injeção utilizada também deve ser considerada. Existem diferentes tipos de máquinas de injeção, e o molde deve ser compatível com a tecnologia utilizada na produção. Isso inclui avaliar a pressão de injeção, a velocidade e o tipo de sistema de resfriamento. A escolha de um molde que não seja compatível com a tecnologia de injeção pode resultar em falhas no processo e produtos de baixa qualidade.
Em resumo, a escolha do molde para injeção plástica envolve uma análise cuidadosa de diversos fatores, incluindo material, design, complexidade da peça, custo, capacidade de produção, manutenção, compatibilidade com o material e tecnologia de injeção. Considerar esses aspectos pode ajudar os fabricantes a tomar decisões mais informadas e a otimizar seus processos de produção, garantindo produtos de alta qualidade e eficiência. A colaboração com uma ferramentaria de moldes plasticos pode ser um passo importante para garantir que as escolhas feitas atendam às necessidades específicas de cada projeto.
3. Processo de Fabricação de Moldes Injeção Plástica
A fabricação de moldes para injeção plástica é um processo complexo que envolve várias etapas, cada uma delas crucial para garantir a qualidade e a precisão do produto final. Desde o design inicial até a produção e testes, cada fase do processo deve ser cuidadosamente planejada e executada. Neste artigo, exploraremos as principais etapas do processo de fabricação de moldes para injeção plástica.
O primeiro passo no processo de fabricação é o design do molde. Nesta fase, engenheiros e designers trabalham juntos para criar um modelo digital do molde, utilizando software de CAD (Desenho Assistido por Computador). O design deve levar em consideração a geometria da peça a ser produzida, as entradas de injeção, os sistemas de resfriamento e outros fatores que podem impactar a eficiência do molde. Um design bem elaborado é fundamental para evitar problemas durante a injeção, como falhas de preenchimento e bolhas de ar.
Após a finalização do design, a próxima etapa é a fabricação do molde. Essa fase geralmente envolve a usinagem de blocos de metal, que podem ser de alumínio ou aço, dependendo das especificações do molde. A usinagem é um processo que utiliza ferramentas de corte para remover material do bloco, criando a forma desejada. É aqui que a precisão é essencial, pois qualquer erro na usinagem pode resultar em um molde que não atende às especificações necessárias. A ferramentaria e usinagem desempenham um papel crucial nesta etapa, garantindo que as tolerâncias sejam mantidas e que o molde seja fabricado com a máxima precisão.
Uma vez que o molde é usinado, ele passa por um processo de montagem. Nesta fase, as diferentes partes do molde são unidas, incluindo as cavidades, as placas de suporte e os sistemas de resfriamento. A montagem deve ser realizada com cuidado para garantir que todas as peças se encaixem corretamente e funcionem como um todo. Qualquer desvio na montagem pode afetar o desempenho do molde e a qualidade do produto final.
Após a montagem, o molde é submetido a um processo de tratamento térmico. O tratamento térmico é utilizado para aumentar a dureza e a resistência do material, o que é essencial para garantir a durabilidade do molde durante o uso. Este processo envolve aquecer o molde a altas temperaturas e, em seguida, resfriá-lo rapidamente. O tratamento térmico ajuda a prevenir o desgaste prematuro e a deformação do molde, prolongando sua vida útil.
Uma vez que o tratamento térmico é concluído, o molde passa por um processo de acabamento. O acabamento é uma etapa importante que envolve a polimento das superfícies do molde para garantir que a peça final tenha um acabamento suave e livre de imperfeições. O acabamento também pode incluir a aplicação de revestimentos especiais que ajudam a reduzir o atrito e a facilitar a liberação da peça após a injeção. Um bom acabamento é fundamental para garantir a qualidade do produto final e a eficiência do processo de injeção.
Após o acabamento, o molde é submetido a uma série de testes. Esses testes são realizados para verificar se o molde atende às especificações de design e se funciona corretamente. Durante os testes, o molde é colocado em uma máquina de injeção e utilizado para produzir algumas peças. Os engenheiros monitoram o desempenho do molde, verificando se há problemas como falhas de preenchimento, deformações ou outros defeitos. Se algum problema for identificado, ajustes podem ser feitos no molde para corrigir as falhas antes de iniciar a produção em larga escala.
Uma vez que o molde passa nos testes, ele está pronto para a produção em larga escala. Nesta fase, o molde é utilizado para produzir as peças plásticas em grandes quantidades. A eficiência do processo de injeção depende da qualidade do molde e da precisão com que ele foi fabricado. Moldes bem projetados e fabricados podem resultar em ciclos de injeção mais rápidos, menor desperdício de material e produtos de maior qualidade.
Por fim, é importante considerar a manutenção do molde ao longo de sua vida útil. Moldes de injeção plástica exigem manutenção regular para garantir que continuem a funcionar de maneira eficiente. Isso pode incluir limpeza, lubrificação e inspeções periódicas para identificar sinais de desgaste. A manutenção adequada pode prolongar a vida útil do molde e garantir que ele continue a produzir peças de alta qualidade.
Em resumo, o processo de fabricação de moldes para injeção plástica envolve várias etapas, desde o design inicial até a produção e testes. Cada fase do processo deve ser cuidadosamente planejada e executada para garantir a qualidade e a precisão do produto final. A colaboração com uma ferramentaria e usinagem especializada pode ser fundamental para garantir que as escolhas feitas atendam às necessidades específicas de cada projeto, resultando em moldes de alta qualidade e eficiência. A atenção a cada detalhe no processo de fabricação é essencial para o sucesso na produção de peças plásticas por injeção.
4. Vantagens da Injeção Plástica na Indústria
A injeção plástica é um dos processos de fabricação mais utilizados na indústria moderna, oferecendo uma série de vantagens que a tornam uma escolha preferencial para a produção de uma ampla variedade de produtos. Desde componentes eletrônicos até utensílios domésticos, a injeção plástica se destaca por sua eficiência, versatilidade e capacidade de atender a diferentes demandas de mercado. Neste artigo, exploraremos as principais vantagens da injeção plástica na indústria.
Uma das principais vantagens da injeção de plástico é a sua eficiência de produção. O processo de injeção permite a fabricação de grandes quantidades de peças em um curto espaço de tempo. Uma vez que o molde é criado, as máquinas de injeção podem operar em ciclos rápidos, produzindo várias peças em minutos. Isso é especialmente benéfico para indústrias que precisam atender a altas demandas de produção, pois reduz o tempo de fabricação e os custos operacionais.
Outra vantagem significativa é a precisão e repetibilidade do processo. A injeção plástica permite a produção de peças com tolerâncias muito apertadas, o que é essencial em setores como a indústria automotiva e eletrônica, onde a precisão é crucial. Os moldes são projetados para garantir que cada peça produzida seja idêntica à anterior, minimizando a variabilidade e garantindo a qualidade do produto final. Essa consistência é um fator determinante para a confiança do consumidor e a reputação da marca.
A versatilidade dos materiais utilizados na injeção plástica também é uma vantagem importante. O processo permite o uso de uma ampla gama de plásticos, cada um com propriedades específicas que podem ser escolhidas de acordo com as necessidades do produto. Isso inclui plásticos rígidos, flexíveis, resistentes ao calor e até mesmo plásticos recicláveis. Essa diversidade de materiais possibilita a criação de produtos com características únicas, atendendo a diferentes requisitos de desempenho e funcionalidade.
Além disso, a injeção plástica é um processo economicamente viável. Embora o custo inicial de fabricação dos moldes possa ser elevado, a produção em larga escala compensa esse investimento. O custo por unidade diminui à medida que a quantidade de produção aumenta, tornando a injeção plástica uma opção econômica para a fabricação de produtos em massa. Isso é especialmente vantajoso para empresas que buscam maximizar seus lucros e reduzir os custos de produção.
A redução de desperdício é outra vantagem significativa da injeção plástica. O processo é projetado para utilizar a quantidade exata de material necessário para cada peça, minimizando o desperdício. Além disso, os resíduos gerados durante a produção podem ser reciclados e reutilizados, contribuindo para práticas de fabricação mais sustentáveis. Essa eficiência no uso de materiais não apenas reduz os custos, mas também ajuda as empresas a atenderem às crescentes demandas por práticas ambientalmente responsáveis.
A facilidade de automação do processo de injeção plástica também é uma vantagem importante. As máquinas de injeção podem ser facilmente integradas a sistemas automatizados, permitindo a produção contínua e a redução da necessidade de intervenção manual. Isso não apenas aumenta a eficiência, mas também melhora a segurança no ambiente de trabalho, reduzindo o risco de acidentes. A automação também permite que as empresas operem com menos mão de obra, o que pode resultar em economias significativas em custos de pessoal.
Outro aspecto a ser considerado é a capacidade de design complexo que a injeção plástica oferece. O processo permite a criação de peças com geometrias intrincadas e detalhes finos que seriam difíceis ou impossíveis de produzir com outros métodos de fabricação. Isso é especialmente útil em indústrias que exigem designs inovadores e funcionais, como a eletrônica e a medicina. A capacidade de criar produtos com formas complexas pode ser um diferencial competitivo importante no mercado.
Por fim, a injeção plástica também oferece opções de acabamento e personalização. As peças produzidas podem ser facilmente pintadas, texturizadas ou revestidas, permitindo que as empresas ofereçam produtos personalizados que atendam às preferências dos consumidores. Essa flexibilidade no acabamento é uma vantagem significativa em um mercado cada vez mais competitivo, onde a diferenciação do produto é essencial para o sucesso.
Em resumo, a injeção plástica apresenta uma série de vantagens que a tornam uma escolha preferencial na indústria moderna. Desde a eficiência de produção e a precisão até a versatilidade dos materiais e a redução de desperdício, o processo de injeção plástica oferece soluções eficazes para atender às demandas do mercado. À medida que as empresas buscam maneiras de otimizar seus processos de fabricação e atender às expectativas dos consumidores, a injeção plástica continuará a desempenhar um papel fundamental na indústria.
5. Manutenção e Cuidados com Moldes
A manutenção adequada dos moldes de injeção plástica é essencial para garantir a eficiência do processo de produção e a qualidade das peças fabricadas. Moldes bem cuidados não apenas prolongam a vida útil do equipamento, mas também minimizam os custos operacionais e reduzem o risco de falhas durante a produção. Neste artigo, abordaremos as melhores práticas de manutenção e cuidados com moldes, destacando a importância de cada uma delas.
Um dos primeiros passos na manutenção de moldes é a limpeza regular. A sujeira, o resíduo de plástico e outros contaminantes podem se acumular nas superfícies do molde, afetando a qualidade das peças produzidas. É recomendável realizar uma limpeza após cada ciclo de produção ou, pelo menos, diariamente, dependendo da frequência de uso. Utilize produtos de limpeza adequados e evite solventes agressivos que possam danificar o molde. A limpeza deve incluir a remoção de resíduos das cavidades, canais de resfriamento e outras áreas críticas.
Além da limpeza, a lubrificação é um aspecto crucial da manutenção. As partes móveis do molde, como pinos e eixos, devem ser lubrificadas regularmente para garantir um funcionamento suave e evitar o desgaste prematuro. A falta de lubrificação pode resultar em atrito excessivo, levando a danos e falhas no molde. Utilize lubrificantes recomendados pelo fabricante e siga as instruções sobre a frequência e a quantidade a ser aplicada.
A inspeção periódica dos moldes é outra prática importante. Realizar inspeções regulares permite identificar problemas antes que se tornem sérios. Durante a inspeção, verifique se há sinais de desgaste, corrosão ou danos nas superfícies do molde. Preste atenção especial às áreas que estão sujeitas a maior pressão e atrito. Se forem identificados problemas, é fundamental realizar os reparos necessários imediatamente para evitar interrupções na produção.
Os ajustes e calibrações também são essenciais para garantir que o molde funcione corretamente. Com o tempo, os moldes podem sofrer deformações ou desgastes que afetam sua precisão. Realizar ajustes regulares ajuda a manter as tolerâncias necessárias para a produção de peças de alta qualidade. Isso pode incluir o alinhamento de componentes, a verificação das dimensões das cavidades e a calibração dos sistemas de resfriamento. A manutenção preventiva é sempre mais econômica do que lidar com problemas após a ocorrência de falhas.
Outro aspecto importante é a proteção contra corrosão. Moldes de injeção plástica são frequentemente expostos a umidade e produtos químicos que podem causar corrosão. Para proteger os moldes, é recomendável aplicar revestimentos protetores e armazená-los em ambientes controlados, onde a umidade e a temperatura sejam mantidas em níveis adequados. Além disso, após a limpeza, é uma boa prática aplicar uma camada de óleo protetor nas superfícies do molde para evitar a oxidação.
A documentação e registro das atividades de manutenção também são fundamentais. Manter um registro detalhado das limpezas, lubrificações, inspeções e reparos realizados ajuda a monitorar o estado do molde ao longo do tempo. Essa documentação pode ser útil para identificar padrões de desgaste e prever a necessidade de manutenção futura. Além disso, pode servir como referência para a equipe de manutenção, garantindo que todos os procedimentos sejam seguidos corretamente.
É importante também considerar a treinamento da equipe que opera e mantém os moldes. A formação adequada dos operadores e da equipe de manutenção é essencial para garantir que todos compreendam a importância dos cuidados com os moldes e saibam como realizar as tarefas de manutenção corretamente. Investir em treinamento pode resultar em uma operação mais eficiente e na redução de erros que podem levar a danos nos moldes.
Por fim, a colaboração com fornecedores e especialistas em manutenção de moldes pode ser extremamente benéfica. Muitas vezes, os fabricantes de moldes oferecem serviços de manutenção e suporte técnico que podem ajudar a garantir que os moldes sejam mantidos em condições ideais. Consultar especialistas pode fornecer insights valiosos sobre as melhores práticas de manutenção e ajudar a resolver problemas complexos que possam surgir.
Em resumo, a manutenção e os cuidados com moldes de injeção plástica são fundamentais para garantir a eficiência e a qualidade da produção. A limpeza regular, a lubrificação, a inspeção periódica, os ajustes e calibrações, a proteção contra corrosão, a documentação das atividades de manutenção, o treinamento da equipe e a colaboração com fornecedores são práticas essenciais que devem ser seguidas. Ao investir tempo e recursos na manutenção adequada dos moldes, as empresas podem prolongar a vida útil do equipamento, reduzir custos operacionais e garantir a produção de peças de alta qualidade.
6. Tendências e Inovações em Moldes de Injeção Plástica
A indústria de moldes de injeção plástica está em constante evolução, impulsionada por inovações tecnológicas e mudanças nas demandas do mercado. À medida que as empresas buscam maneiras de otimizar seus processos de produção e atender às expectativas dos consumidores, novas tendências e inovações estão surgindo. Neste artigo, exploraremos algumas das principais tendências e inovações em moldes de injeção plástica que estão moldando o futuro da indústria.
Uma das tendências mais significativas é a automação e digitalização dos processos de fabricação. A introdução de tecnologias como a Internet das Coisas (IoT) e a Indústria 4.0 está transformando a maneira como os moldes são projetados, fabricados e mantidos. Sensores e dispositivos conectados permitem monitorar o desempenho dos moldes em tempo real, coletando dados sobre temperatura, pressão e ciclos de produção. Essa coleta de dados pode ser utilizada para otimizar o processo de injeção, identificar problemas antes que se tornem críticos e melhorar a eficiência geral da produção.
Outra inovação importante é o uso de materiais avançados na fabricação de moldes. Tradicionalmente, os moldes eram feitos principalmente de aço e alumínio, mas agora há uma crescente adoção de materiais como plásticos de engenharia, compósitos e até mesmo materiais reciclados. Esses novos materiais oferecem vantagens como menor peso, resistência à corrosão e maior flexibilidade no design. Além disso, a utilização de materiais reciclados contribui para práticas de fabricação mais sustentáveis, alinhando-se às crescentes demandas por responsabilidade ambiental.
A impressão 3D também está se tornando uma ferramenta valiosa na fabricação de moldes de injeção plástica. A impressão 3D permite a criação rápida de protótipos e moldes, reduzindo significativamente o tempo e os custos associados ao desenvolvimento de novos produtos. Com a impressão 3D, os fabricantes podem testar e ajustar designs antes de investir na produção de moldes tradicionais, resultando em um processo de desenvolvimento mais ágil e eficiente. Essa tecnologia também possibilita a produção de geometrias complexas que seriam difíceis de alcançar com métodos convencionais.
Além disso, a personalização em massa está se tornando uma tendência crescente na indústria de injeção plástica. À medida que os consumidores buscam produtos que atendam às suas necessidades específicas, as empresas estão se adaptando para oferecer opções personalizadas. Isso requer moldes que possam ser facilmente ajustados ou modificados para produzir diferentes variantes de um produto sem a necessidade de criar novos moldes do zero. A flexibilidade no design e na produção é essencial para atender a essa demanda crescente por personalização.
A eficiência energética também é uma preocupação crescente na indústria de moldes de injeção plástica. Com a pressão para reduzir custos e minimizar o impacto ambiental, as empresas estão investindo em tecnologias que melhoram a eficiência energética dos processos de injeção. Isso inclui a adoção de máquinas de injeção mais eficientes, sistemas de resfriamento otimizados e o uso de moldes que minimizam o desperdício de material. A eficiência energética não apenas reduz os custos operacionais, mas também contribui para a sustentabilidade da produção.
Outra inovação relevante é a integração de sistemas de controle avançados nos moldes. Esses sistemas permitem um monitoramento mais preciso e em tempo real do processo de injeção, possibilitando ajustes automáticos durante a produção. Isso resulta em uma maior consistência na qualidade das peças produzidas e na redução de defeitos. A automação dos processos de controle também libera os operadores para se concentrarem em tarefas mais estratégicas, aumentando a eficiência geral da operação.
Por fim, a colaboração entre empresas e centros de pesquisa está se tornando cada vez mais comum na indústria de moldes de injeção plástica. Parcerias entre fabricantes de moldes, empresas de injeção e instituições acadêmicas estão impulsionando a pesquisa e o desenvolvimento de novas tecnologias e processos. Essa colaboração permite que as empresas se mantenham atualizadas com as últimas inovações e tendências, garantindo que possam competir de maneira eficaz no mercado global.
Em resumo, as tendências e inovações em moldes de injeção plástica estão moldando o futuro da indústria, impulsionadas pela automação, digitalização, novos materiais, impressão 3D, personalização em massa, eficiência energética, controle avançado e colaboração. À medida que as empresas adotam essas inovações, elas não apenas melhoram seus processos de produção, mas também atendem às crescentes demandas dos consumidores por produtos de alta qualidade e sustentáveis. O futuro da injeção plástica promete ser mais eficiente, flexível e alinhado com as necessidades do mercado.
Em conclusão, os moldes de injeção plástica são fundamentais para a indústria moderna, oferecendo uma combinação de eficiência, precisão e versatilidade na produção de uma ampla gama de produtos. Ao entender os diferentes tipos de moldes, os fatores a serem considerados na escolha, o processo de fabricação e as vantagens da injeção plástica, as empresas podem tomar decisões informadas que otimizam sua produção. Além disso, a manutenção adequada e a adoção de tendências e inovações emergentes são essenciais para garantir a longevidade e a eficácia dos moldes. Com essas práticas, é possível não apenas atender às demandas do mercado, mas também se destacar em um ambiente competitivo, assegurando a qualidade e a sustentabilidade dos produtos fabricados.